Design Features
Hayward Tyler canned motor pumps offer a combined pump and motor on a common shaft, wrapped in a pressure boundary. This eliminates the need for mechanical seals and hence eliminates the chance of a process fluid leak, making it a highly reliable solution for critical applications.
- Thrust bearing provides reliability during upset pump conditions
- No mechanical seal means no leakage
- Inherently safe
- Double layer pressure boundary containment
- Self-lubricated bearings – no external lubrication system needed
- Eliminates pump and motor alignment – common shaft
- Low noise
Codes & Specifications
Operating Data
MOTOR | US | SI |
---|---|---|
Power | 5-450*HP | 3-335*kW |
Voltage | 380-575V | 380-575V |
Poles | 2, 4 | 2, 4 |
VFD Compatible | Yes | Yes |
Design Pressure | 0-6000+psig | 0-415 bar |
Design Temperature | -184 to 750ºF | -120º to 400ºC |
PUMP | US | SI |
---|---|---|
Flow | Up to 3,000* USgpm | 680*m3/hr |
Head | Up to 1000*ft | 305*m |
Codes and Compliances:
- ASME Section VIII and III including stamp (N)
- Hydraulic Institute
- Pressure Equipment Directive (PED)
- 10CFR21 and 10CFR50 (Nuclear)
- RCC-M and RCC-E
- Other international codes as required
Applications
Hayward Tyler Engineered Canned Motor Pumps are ideal for the following typical plant applications:
NUCLEAR
- Reactor Water Clean-Up (RWCU)
- Fuel pool
- Heavy water transfer/collection
- Main coolant pump
- Blow Down System Drain/Recirculation
- Emergency diesel fuel transfer
- Radwaste
- Spent fuel pool aux cooling system
- Reactor coolant drain
CHEMICAL / PETROCHEMICAL
- Acids
- Ammonia
- Benzene
- Butenol
- Caustic
- Crude Ester
- Formaldehyde
- Heat transfer oils (Dowtherm, Therminol, Texatherm, etc.)
- Hydrogen Sulfide
- Nickel Catalyst
- Nitroparafins
- Olifins
- Reactor circulation/injection
- Titanium tetrachloride
Ideal for fluids with the following properties:
- High volatility
- Carcinogenic
- Corrosive
- Lethal
- High temperature
- Low temperature
- Radioactive
- Polymerizing
Documents
Download our brochures to read more about all Hayward Tyler Engineered Canned Motor Pumps
Download case studies related to Hayward Tyler Engineered Canned Motor Pumps
Our team is ready to discuss your project.
Let’s talk about your performance-critical application.
Contact us:
Learn more about our sealless, zero-leakage pumps and motors for robust and reliable performance.
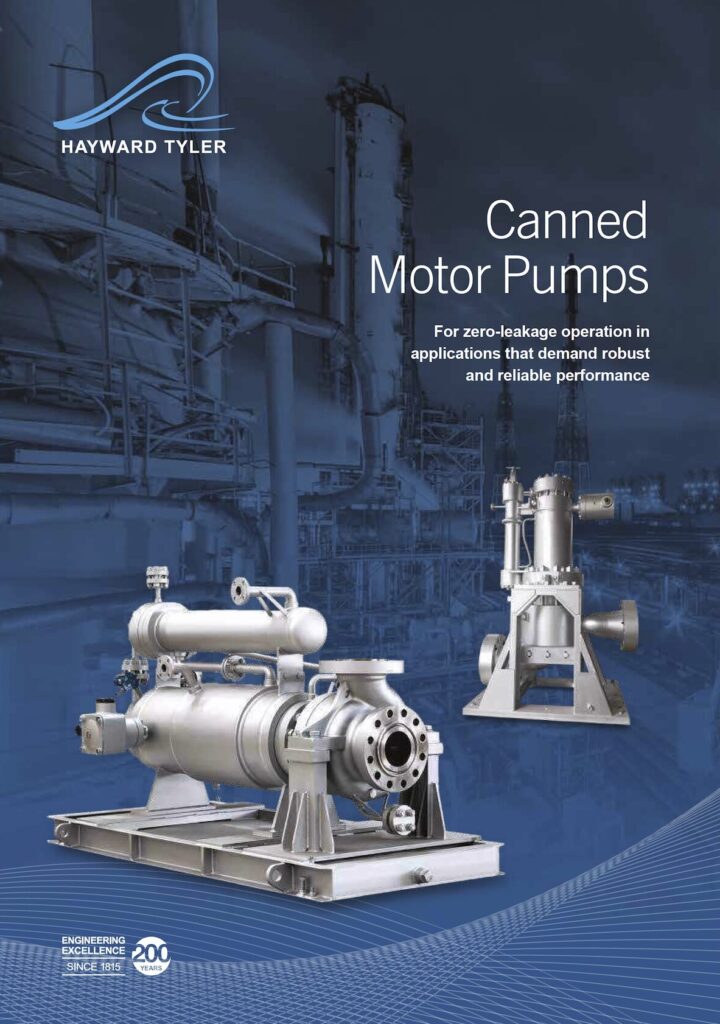
Sectional Arrangement
Hover over the numbers below for details about each feature.
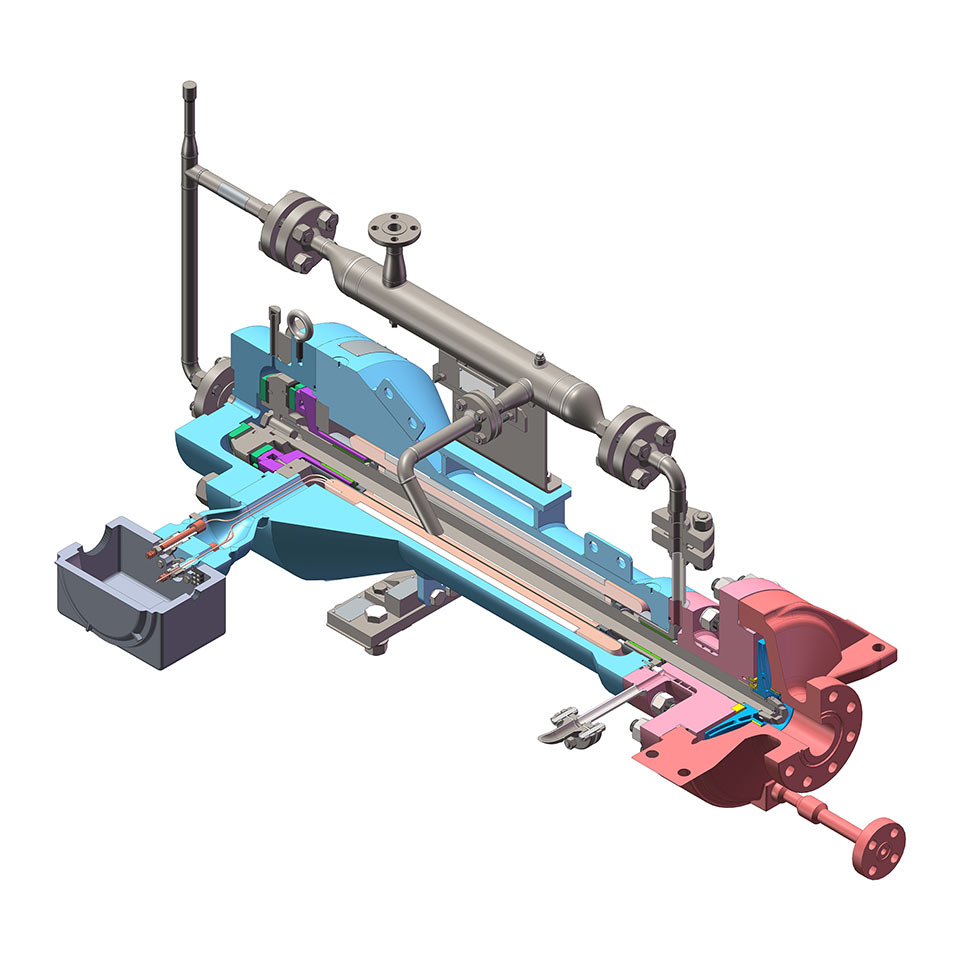






















Service & Support
We take great pride in supporting our clients across the globe with timely service. We cover all aspects of support that might be needed during the lifecycle of your Hayward Tyler pump and/or motor.
We provide:
- 24/7/365 Technical Support
- Engineering
- Spare Parts
- Repairs
- Training
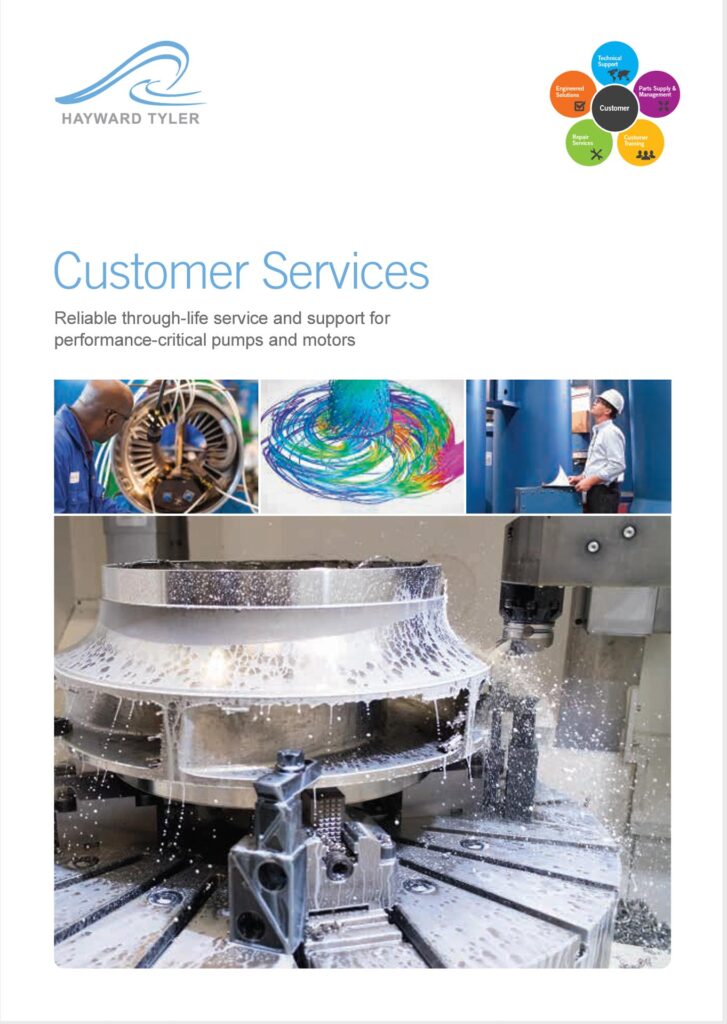
Canned Motor Pump FAQs
A canned motor pump is a type of centrifugal pump where the pump and motor are integrated into a single, sealed unit. The pump and motor combination are leak-free, making them suitable for pumping hazardous liquids as they will not leak into the atmosphere.
What is a canned motor pump used for?
Our canned motor pumps are ideal for applications that require the highest reliability, safety, and performance, as our pumps are leak-free and low maintenance. They are used in a variety of industries—such as petrochemical, chemical refinement and processing, hydrogen and clean energy, refrigeration, renewables, and nuclear—to move large amounts of fluid.
Why choose a canned motor pump over other options?
Canned motor pumps are preferred over mechanically sealed pumps and magnetic drive pumps for a number of reasons. Lack of seals eliminates failures and safety issues that seals can cause. They are are also low maintenance and reduce noise levels. They also weigh less than other pumps, eliminating the need for a foundation, and eliminate problematic emissions inspections and reporting associated with other pump types.
How is the seal eliminated in these pumps?
Due to the laws of physics, higher-pressure fluids want to move to lower-pressure areas. Because traditional pumps must couple to a driver (motor or turbine), the shaft needs to exit the pump pressure boundary (pump case). This means the high-pressure fluid created by the rotating pump wants to leak into the atmosphere along the shaft penetration. This is stopped in traditional pumps by using gland packing or a mechanical seal. CMPs and BCPs use a different approach by using a common shaft for the pump and motor and containing it all in a pressure boundary. This eliminates the pressure differential across the rotating seal and the driving force for the fluid to leak.
What type of material(s) are canned motor pumps made from?
Canned motor pumps are typically made from type 304 stainless steel for wetted components, with the stator and rotor cans constructed from Hastelloy C276 for its high corrosion resistance and efficiency. Gaskets are usually made of PTFE or spiral-wound stainless steel, depending on temperature and pressure conditions. Bearings are typically made from carbon graphite or silicon carbide, chosen based on application requirements.
Are these pumps environmentally friendly?
Our CMPs and BCPs are inherently safe and environmentally friendly. Because they are sealless, the danger of a fluid leak is eliminated, preventing contamination to the environment.
How long do these pumps last?
Our CMPs and BCPs can last up to 30 years, but typically last 10 to 15 years. The lifespan is dependent upon fluid properties and operating conditions.
Highlights from our Knowledge Base
Our Knowledge Base can help answer your questions on a variety of topics with a wealth of pumps and motors information. With tools such as webinars, white papers, case studies, service bulletins, product knowledge, and a database of downloads, brochures, and sheets, our expertise is your competitive advantage.