Download this Case Study:
Utilizing advanced scanning and computer analysis to validate the performance of impellers from a repaired pattern
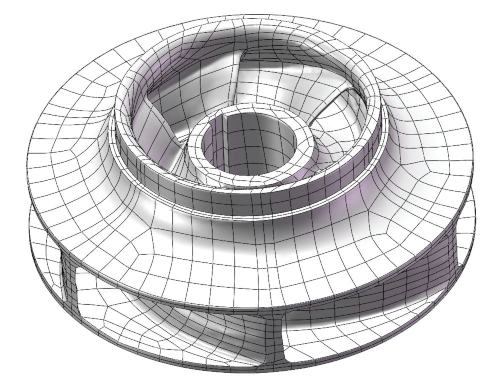
Hayward Tyler supplied a replacement impeller for use in a Nuclear Safety Related Component Cooling Water application within a nuclear power plant. The original equipment was supplied in the early 1970s and the original pattern used to cast the impellers had been subject to degradation through the years. In order to validate the pattern repairs and avoid large-scale performance testing, Hayward Tyler used computer modelling and analysis to validate the refurbished pattern and impellers produced from it.
The refurbished pattern was used to pour a new impeller that was machined complete to the original drawings. The impeller was dimensionally inspected and then sent to Shape Fidelity, an industry leading inspection company, to create a 3D Computer Aided Design (CAD) model. Traditional 3D scanning of impellers can be difficult, given the sweeping vane geometry and blind internal surfaces. This can require the CAD modeler to interpolate geometry that cannot be scanned in the center of the hydraulic passage, causing differences between the model and actual impeller geometry. Given the importance of the entire hydraulic passage to generate the required duty, a new proprietary technique was used to scan the entire passage and create the model. This new technique is non-destructive, and provides data for all surfaces.
Hayward Tyler engineers combined the 3D CAD model with the pump case model and other key features of the original pump to create the entire fluid body, which was then exported to be analyzed using Computational Fluid Dynamics (CFD) software. They used their NQA-1 Commercial Dedication Program to validate the CFD software. The results of the CFD were compared to the original test pump curves and proved that the finish machined impellers, based on the pattern modifications, would meet the original contract requirements.
The entire process, from the start of scanning to completed and validated CFD results, took less than 2 weeks. This new approach can be used to validate pattern changes, reverse engineer existing equipment, or upgrade existing equipment, all without the need to performance test.
Project Summary
SITE/LOCATION:
- USA
SCOPE OF WORK:
- Refurbishment of a legacy impeller pattern
- Finish machined impeller produced from a refurbished pattern
- Advanced scanning techniques to produce CAD model of the actual impeller
- Computational Fluid Dynamics(CFD) analysis using Simerics PumpLinx®
- NQA-1 Commercial Dedication of CFD Software
- Validated modifications to pattern by comparing CFD result to original test curves
BASIC PUMP/MOTOR DESIGN DETAILS:
- Type D, Horizontally split case, double suction pump, 8x10x16 DI
- Rated Flow: 3,500 USgpm
- Rated Head: 179 ft
- Design Pressure: 150 psig
- Design Temp: 160 ° F
- Driver: AC Motor, 200 hp, 1800rpm
- Power Supply: 4000 V/ 60 Hz / 3 ph
- Designed and manufactured in Colchester, VT
Project Data Sheet
Product | Component Cooling Water, Double Suction Pump |
Quantity | Eight (8) |
Codes and Standards
Design | ASME Section III 1971 Class 3 Winter Addendum 1971 |
Flange Standard | ANSI B16.5 |
Materials Standard | ASME / ASTM |
Nozzle Loading | Customer Defined |
Pump Details
Pump Type | 10” Suction x 8” Discharge with 16” Double Suction Impeller |
Fluid Pumped | Demineralized Water |
Operating Temperature | 160 °F (71 °C) |
Rated Flow | 3500 USgpm (795 m3 / hr) |
Rated Head | 179 ft (55m) |
Specific Gravity | 1.0 |
Design Pressure | 150 psi (10 bar) |
Design Temperature | 160 °F (71 °C) |
Impeller Material | ASTM A216 WCB |
Pump Case Material | ASME SA216 WCB |
Motor Details
Motor Rating | 200 HP (150 kW) |
Service Factor | 1.25 |
Nominal Speed | 1800 rpm |
Power Supply | 4000 V / 3 ph / 60 Hz |
Weights (Approximate Dry)
Rotating Element | 380 lbs (172 kg) |
Pump | 1500 lbs (680 kg) |
Pump and base | 3950 lbs (1792kg) |