With a wide range of capabilities, this facility provides full machining as well as 24/7/365 support, repairs and refurbishment for pumps and motors.
With 68,000 square feet of manufacturing space, our Luton, England location offers a variety of options to serve your pump and motor needs. We design, manufacture, install, service, test, refurbish, and repair rotating equipment/machinery, valves, and pressure vessels for power, nuclear, water, gas, oil, and chemical industries. Throughout our work, we take a hands-on approach to parts and supply management, closely managing details and deadlines to ensure our customers continue to choose us for their mission-critical pumps and motors.
We adhere to strict quality standards such as ISO 9001, Pressure Equipment Directive (PED), and BE EN ISO 3834—and our inspection department is equipped with state-of-the-art technology that allows us to reverse engineer outdated parts.
Contact Hayward Tyler – Luton, England
Our engineering, technical support, and repairs/refurbishment teams are ready to talk to you. Get in touch with us and we’ll help connect you to the right person.
Get in touch:
Key Facility Capabilities
- New units, spare parts, shop service, and field service
- Design engineering support
- Fabrication, milling, turning, and boring capabilities
- State-of-the-art winding facility
- Injection moulding technology for high pressure application
- BCP Performance testing to allow upwards of 4200m3/hr flow at 25bar pressure
- Low and High voltage – up to 32kV
- 3.2MW and 6MW supply variable speed drive system for 0 – 125Hz frequency testing
- ISO Class 9 certified clean assembly room with integrated push pull system and particulate monitoring
- Complete overhaul/repair to OEM
specification - Overhaul/repair of competitors BCP and submersible motors
- Designated repair facility with reverse engineering capabilities
- ISO Class 9 clean assembly & test: net positive suction head (NPSH), no-load test, load performance testing, hydrostatic pressure testing (400 bar rated), hotbed test
Featured Services
Repair & Maintenance
Developing wet wound motor technology has extended to HV and LV motors of non-HT design being part of the Luton repair capability. The transference of high spec wet wound motor technology moves past wind and into jointing, connect, termination, and into bearing technology, materials, and beyond. To support in the field, HT Luton has a Global response capability providing customer support expertise through qualified engineers.
Testing
We provide testing to ensure your pumps and motors perform to the requirements of your application. Our testing capabilities have direct online (DOL) power supply: 11kV 2.4MW. We can identify and diagnose operational issues, motor load tests, and hydrostatic pressure tests up to 1600Bar. We also have 8 channel vibration measurement and noise testing and use advanced techniques, such as special analysis and modal analysis, so that we can precisely monitor and detect issues. As an OEM, we have the capabilities for all of your testing needs.
Engineering Excellence
Our 20+ strong engineering team comprising of highly skilled and experienced mechanical, hydraulic, electrical, and production engineers with a heritage of designed pumps and motors for the most severe service applications and markets.
Fully equipped with the following software capabilities, our engineering team can meet any customer design requirements:
- Solidworks – 3D CAD design
- Ansys Maxwell – Electrical Simulation
- CF Turbo / Simerics – Computational Fluid Dynamics (CFD) for hydraulic flow simulations
- XLrotor – Lateral & Torsional dynamic simulation.
- Finite Elements Analysis (FEA) – Structural analysis
- Motor CAD – Thermal Motor analysis
All designs meet as default ASME, PED, or customer-specific pressure standards and quality requirements such as API610 and IBR.
Hayward Tyler are proud supporters of the Institute of Mechanical Engineers and the Institute of Engineering Technology and have a number of Chartered Engineers in the team.
Reverse Engineering
With significant investment in reverse engineering technology, we can now service and repair a wide range of Hayward Tyler legacy products along with competitor products. Fully integrated into our design engineering team, our world-class scanning technology is used to provide fast solutions to existing field hardware. This is converted into a Solidworks model and drawing, which can then be used to purchase replacements to meet a rapid turnaround for our customers. All designs are reviewed by an experienced mechanical design team, along with analysis to improvement design parameters whenever possible. All of which leads to the best possible product solution for our customers.
New Product Development
At Hayward Tyler, innovation is one of our core values. This has allowed us to be the inventors of many world-firsts, including the gland-less boiler circulating pump and submersible motors. This culture of innovation, utilizing our vast experience and technical expertise, has allowed Hayward Tyler to continually evolve and stay at the forefront.
We have an independent NPD Team solely focused on innovation, enabling us to adapt to our customers’ demands by creating new products, developing existing products, and researching new technologies. We hold various patents for the techniques and processes we have developed for building performance critical motors and pumps, allowing us to provide world-class engineering solutions for the harshest of environments.
Technical Support
Our design engineering team is experienced in analyzing complex engineering problems in pumps and motors — a critical requirement for technical support that addresses your most demanding operational issues.
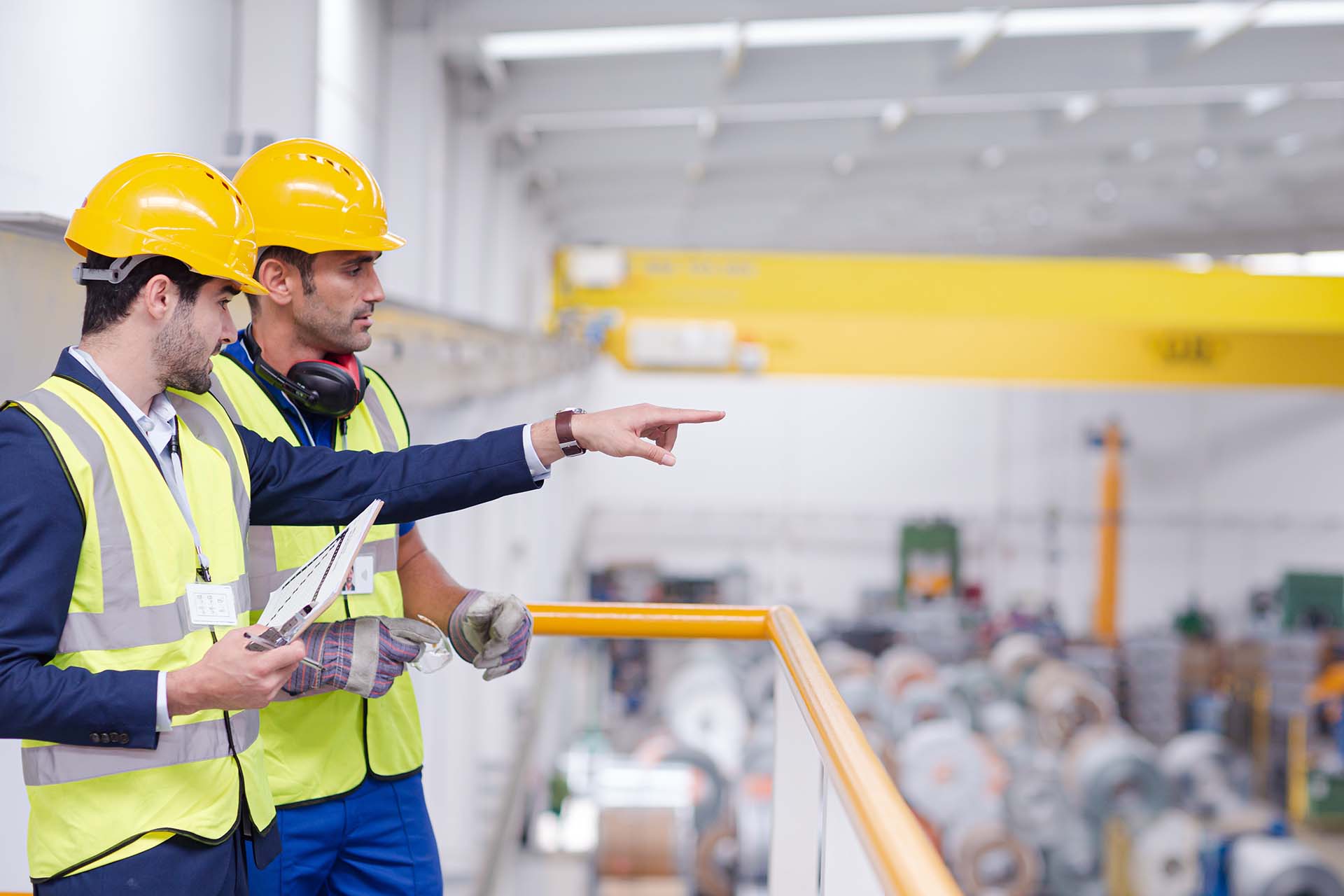
Health & Safety
A commitment to safety ensures the success of our workforce
Safety is at the core of everything we do, with regular health and safety training and certifications integrated into our daily culture at Hayward Tyler Luton. Our staff is provided with the tools to maintain high-level safety practices, maintain their health and well-being, and proactively prevent risk and accidents whether on or off-site.
Testing Capabilities
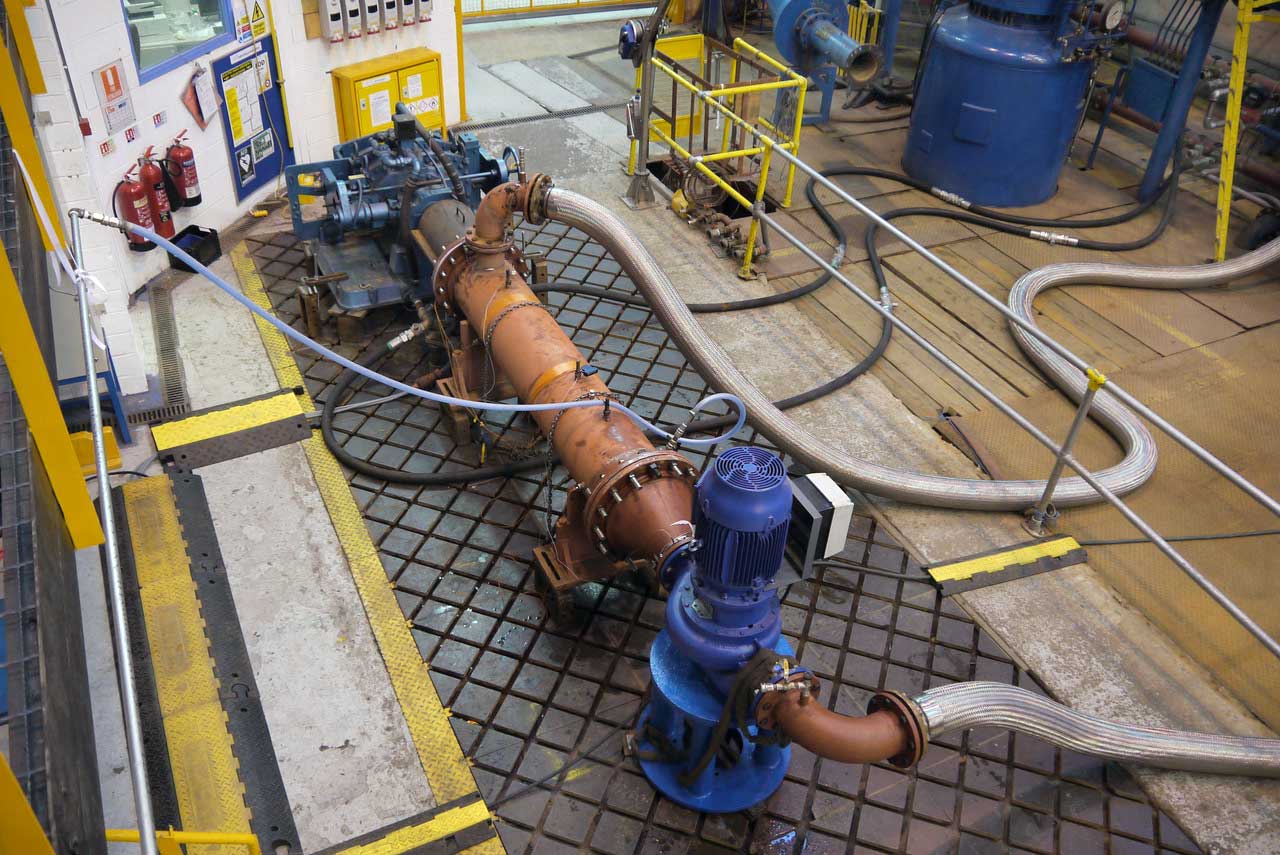
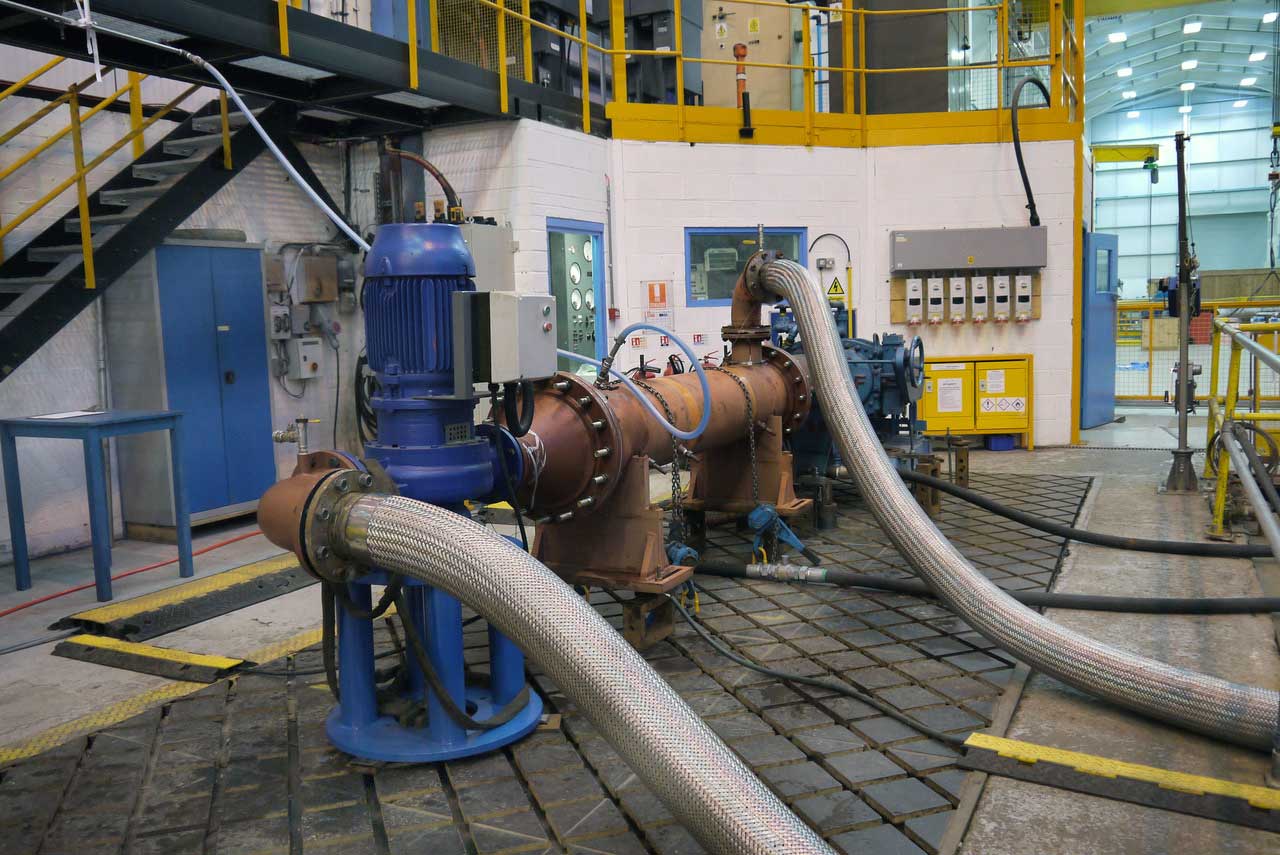
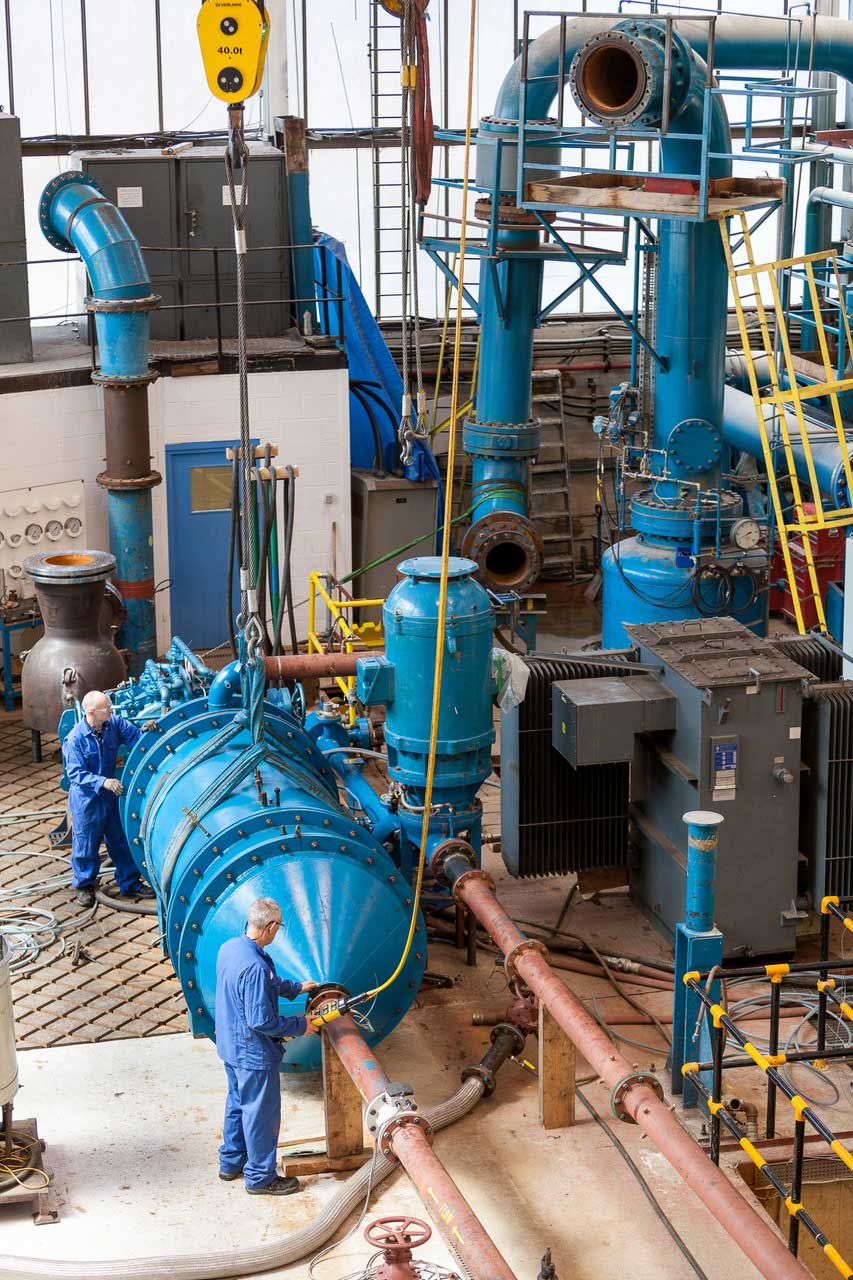
- Direct online (DOL) power supply: 11kV 2.4MW
- 6MW, 0-6.6Kv @ 0-120Hz VFD Drive
- Maximum Flow rate: 4,200m³/h (1.1 million gph US) and maximum head of 25 Bar (363psi)
- Motor load test up to 6.7MW, 3600RPM
- Hydrostatic pressure test up to 1600Bar
- Test Pits – Ranging between 3m to 7.5m Deep
- IR (up to 5kVDC) and HIPOT (up to 30kVAC)
- 8 Channel Vibration measurement and noise testing
- PD Test Lab up to 50kV
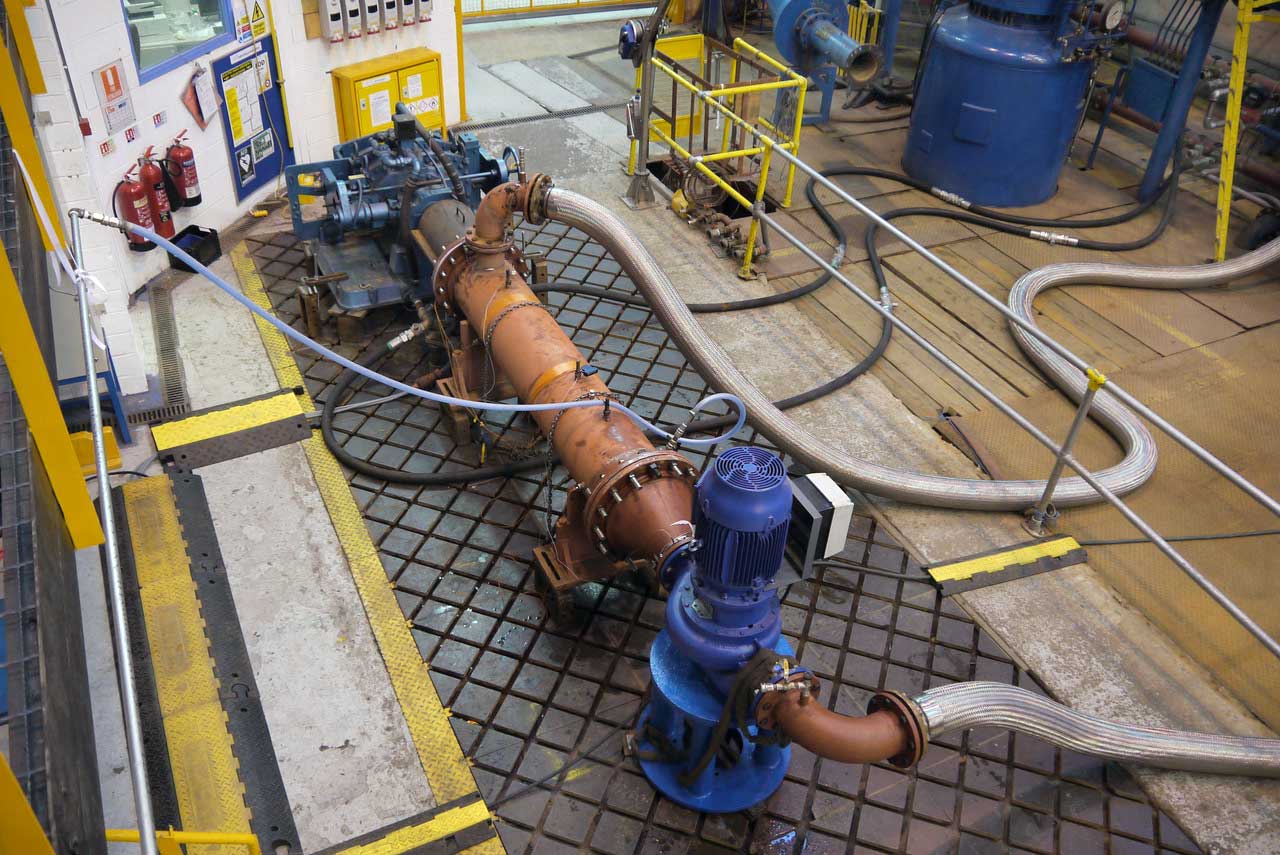
Certifications and Quality
Our Certifications
Our Quality Policy
At Hayward Tyler Luton, we are dedicated to understanding the needs and exceeding the expectations of our customers and stakeholders. We do this by aligning strategies with business goals, prioritizing safety, consistently delivering high-quality products on time, and continually improving our service, quality, and processes—all while maintaining compliance with regulations and fostering clear communication at all levels.
Capability Statement
Our one-page capabilities sheet outlines company information, core competencies, and differentiators for this facility.
Facility Features
Square Feet of Manufacturing Space
Years in Operation
Employees on our Luton Engineering Team
Trusted provider of repairs and upgrades
We continue to exceed customer demands for pump and motor testing, precision manufacturing, and repair turnaround times.
Workforce
We work hard to promote a positive and highly-productive workforce culture, and to ensure that each member of our team is driven by a shared commitment to quality, integrity, and efficiency. This workforce dedication keeps us strong and results in reliable outcomes for our customers.
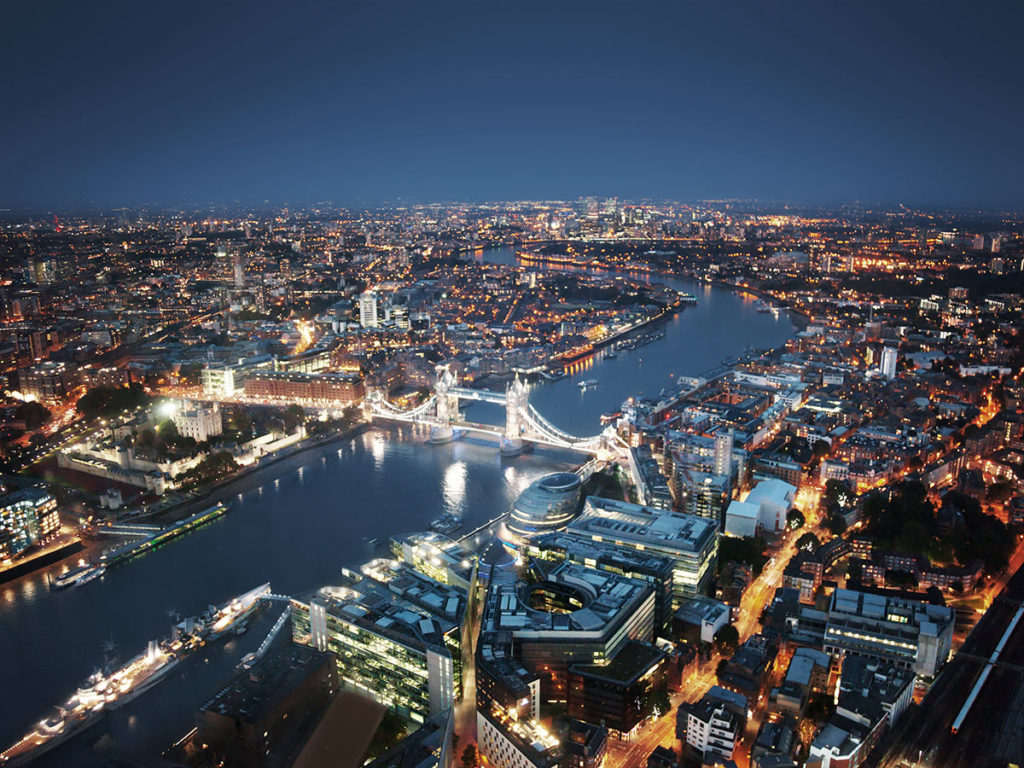