Download this Whitepaper:
National Lab Extends Contract with Hayward Tyler for Equipment Supply and Engineering Services
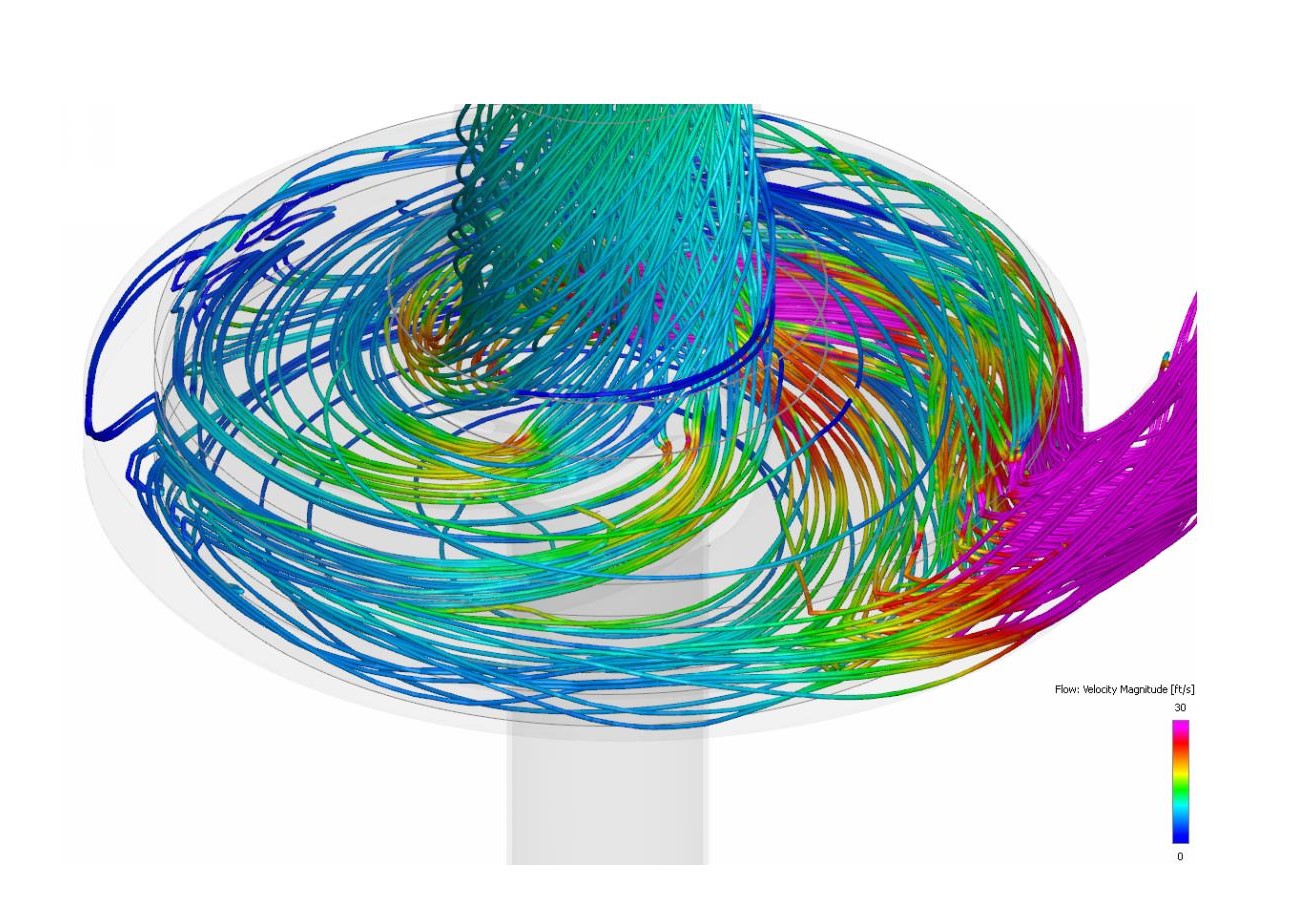
Hayward Tyler, Inc. (HTI) designed, manufactured and supplied canned motor type primary coolant pumps for nuclear reactor (NR) flowing water test loops at a US national laboratory. The loops are designed to test reactor fuel and structural material for the NR program and support the continuing need for irradiation test data. Within the test loop, the coolant pumps are installed in series. When a newly determined operating scenario was identified in which the canned motor pump would wind-mill for extended periods of time (windmilling is when fluid is pumped through the non-energized canned motor pump), Hayward Tyler was asked to conduct an engineering study to determine if the as-built reverse thrust bearing was suitable for use during this scenario.
To evaluate the suitability of the bearing to operate under these conditions, two analyses were required: The first was a computational fluid dynamics (CFD) analysis to determine the rotational speed and axial load that the bearing would be subjected to under wind-milling conditions. The second was an analysis of the reverse thrust bearing to determine if it can maintain fluid film lubrication when operating at the speed and loading determined from the CFD analysis. Maintaining lubrication is required to prevent excessive wear and premature failure of the reverse thrust plate material. The CFD analysis was performed by Hayward Tyler’s design engineers. The bearing analysis was performed in conjunction with an external partner that specializes in bearing performance evaluations.
The results of the bearing analysis predict that the reverse thrust bearing will be able to operate under wind-milling conditions indefinitely without risk of damage or wear to the bearing. After completing the engineering analyses, HTI conducted a 30-hour performance test of a similar canned motor primary coolant pump under wind-milling conditions at Hayward Tyler’s Colchester, VT facility. The thrust bearing was examined post-test and showed no wear.
Project Summary
SITE/LOCATION:
- Colchester, VT, USA (Engineering and Testing site)
SCOPE OF WORK:
- Computational fluid dynamics (CFD) analysis using Simerics PumpLinx®
- Scenario analysis based on various flow rates and water temperatures
- Head loss calculations
- Thrust bearing performance calculations
- 30-hour perforoamnce test at Hayward Tyler under wind-milling conditions
- Results summarised in an engineering report
BASIC PUMP/MOTOR DESIGN DETAILS:
- Vertical Canned Motor Pump of Centrifugal Volute Design
- Rated Flow: 300 USgpm
- Rated Head: 375 ft
- Design Pressure: 2500 psig
- Design Temp: 650 ° F
- Rated Power: 60 hp
- Power Supply: 460 V/ 60 Hz / 3 ph
Project Data Sheet
Product | Canned Motor Pump |
Quantity | Four (4) + One (1) spare |
Codes and Standards
Design | ASME Section III , Div. 1, Subsec. ND, Cl.3 |
Test Standard (Hydro) | ASME Section III , Div. 1, Subsec. ND, Cl.3 |
Test Standard (Performance) | HI 14.6 |
Test Standard (Vibration) | Customer Defined |
Flange Standard | Grayloc |
Electrical Standard | IEEE 252 / NEMA MG1 |
Nozzle Loading | Customer Defined |
Pump Details
Pump Type | Centrifugal, Single Suction, Single Discharge |
Pump Size | 4″ Suction x 3″ Discharge with 11″ Impeller |
Fluid Pumped | Demineralized Water |
Rated Flow | 300 USgpm (68 m3 / hr) |
Rated Head | 375 ft (115m) |
Specific Gravity | 0.68 |
Design Pressure | 2500 psi (172 bar) |
Design Temperature | 650 °F (343 °C) |
Motor Details
Motor Rating | 60 HP (45 kW) |
Service Factor | 1.0 |
Nominal Speed | 3490 rpm |
Power Supply | 460 V / 3 ph / 60 Hz |
Categories: Case Studies