This service bulletin has been written as a response to questions regarding insulation resistance (IR) and to clarify how to interpret measured values of IR for wet stator motors.
There are many factors that influence IR measurements such as temperature, relative humidity, insulation cleanliness (surface tracking) and measurement equipment. IR measurements are therefore variable and should only be used as an indicative measurement to determine the material/unit insulation properties when new or to monitor IR trend over the life of a product.
Summary
The insulation resistance test is an electrical test which uses a voltage to measure insulation resistance recorded in Ohms. The measured resistance indicates the condition of the insulation between two conductive parts. An infinite resistance would indicate a perfect insulator, but no insulator is perfect, so the higher the reading the better the insulator.
A low resistance between live conductors and earth is an indication of a potential earth leakage in the motor insulation. The earth is typically the motor case. Testing is done with the insulated conductors in conductive fluid (water).
The test current measured consists primarily of three current components:
1. surface leakage current
2. capacitive charging current
3.conduction current
The insulation acts as the dielectric of a capacitor and draws a capacitive charging current. Under direct voltage, the capacitive charging current becomes negligible after ~1 minute, taking the readings after this time will prevent this current from affecting the measurement. Absorption or Polarization current can also be a factor but on XLP insulation this current is negligible which also excludes the use of Polarization Index measurement. Surface leakage current can also be present if the insulation surface between the conductor and the earth is not clean or is wet.
IR measurements are made on new and used units as a quality control method to ensure that there is no significant leakage to earth.
IR measurements are also taken to monitor the insulation ‘health’ of a motor during the installed life and it is important to control the factors which influence IR measurement so that trend can be meaningful. The same test equipment should be used and tests should be done with the motor at a similar temperature and ambient humidity. If IR measurements could not be performed at the same temperature, then the temperature correction method should be applied. See the next section for details.
Hayward Tyler recommends that IR measurements are recorded from the unit commissioning date (or as soon as IR values can be recorded) and over the lifetime of a unit using the chart shown below. IR values should be trended over time after being corrected to 20oC.
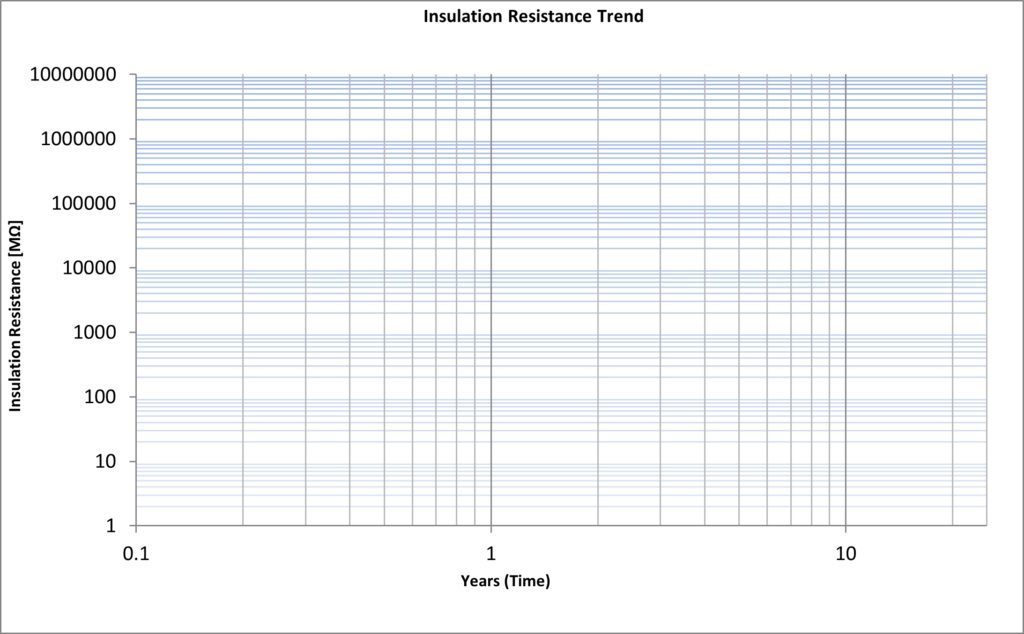
Factors that influence IR measurement
Temperature – When the IR is measured at a higher ambient temperature (e.g. 40°C, 50°C), temperature corrections shall be made in accordance with IEEE Std. 42. For every 10°C increase, the IR value should be halved. Similarly for every 10°C drop, the IR should be doubled.
Surface condition of insulating material – All material must be free of all contaminants including oil and grease to prevent surface tracking. Before an IR measurement is taken at the end connection it is advisable to clean the surface with acetone or a similar product to ensure a contaminant-free surface. Allow sufficient time for the cleaner to evaporate prior to carrying out the test.
Moisture content – Before an IR reading is made on a motor or stator, the Terminal Gland Moulding (TGM), or other end connection, must be free of any obvious moisture. The terminal box must also be free of any moisture as this will also influence the IR reading.
Humidity – Humidity has a significant influence on IR readings depending on the test equipment used. From the analysis of recently recorded results, when relative humidity is above 65%, IR values significantly drop due to moisture, reference the below graph. Hayward Tyler, therefore, does not take IR measurement above 65%, as this does not provide a true IR value. These results will vary in accordance with the climate in which the measurements are taken.
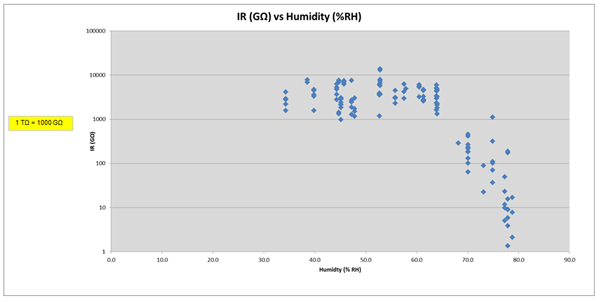
Submergence in water – When the insulation material is immersed in water, the volume resistivity and surface resistivity will change. The surface resistivity will change immediately on contact with water, while the volume resistivity will change in the longer-term depending on the water absorption rate. This will result in a lower IR reading compared to a measurement in a dry condition.
- Volume resistivity is a measure of the resistance of an insulator to the conduction of current.
- Surface resistivity is defined as the electrical resistance of the surface of an insulator material. It is measured from electrode to electrode along the surface of the insulator.
Typical guidance on IR values
IEEE 48 test standard recommends that the minimum IR value can be obtained from the following equation; IR1min = kV+ 1 [MΩ]. However, the IEEE48 recommendation on the minimum insulation resistance is derived from the specification of air-cooled motors. The minimum insulation resistance value for water-filled motors and stators are defined, based on Hayward Tyler’s experience, in the relevant Operating & Maintenance Manual or ENS-81 “Electrical Testing and Acceptance Criteria for Terminal Glands, Wet Stators, and Motors”.
Typical values are:
- New or rewound, unused stators and motors shall have a minimum insulation resistance of 10 Giga Ohm.
- Used stators and motors shall have a minimum insulation resistance of 200 Mega ohms.
- In-service motors shall have minimum insulation resistance of 5 to 20 Mega ohm, depending on the motor. Reaching minimum insulation resistance value indicates that the motor winding has deteriorated to a level where maintenance is required.
- A significant drop in insulation resistance between readings (high rate of IR change) could indicate a developing problem and should be monitored. For example, insulation resistance should not fall to below 200 Mega Ohm at 20 °C from new condition (10 Giga ohm minimum) in less than 12 months.
Conclusion on IR measurement
Motor insulation resistance will deteriorate with time and will depend on insulating material condition, storage and service conditions.
Insulation resistance measurements should be conducted regularly over a period of time to determine an insulation resistance trend. The insulation resistance trend is only an indicative measurement indicating the condition of a winding insulation, insulation resistance measurement is not an exact science. It must be stressed that a low IR reading does not necessarily indicate that a unit is at risk as there are a number of factors that influence IR measurement.
If in doubt, regarding IR measurement values, contact Hayward Tyler below for advice.