This Safety Bulletin is in response to customers asking about the suitability of hardware on connection flanges after return from shop service or upon initial receipt of a new motor. The below information serves as guidance about what needs to be replaced by the customer prior to placing the BWCP in service.
The 6 typical flanges on HT BWCPs, which are:
(1) motor case to pump case
(2) motor case to motor cover
(3) lower fill and drain port
(4&5) two heat exchanger connections
(6) motor purge (mostly on older designs)
SRVB11 describes HT’s methods of restoring and preparing these flanges for installation and advising of the customer’s responsibility when the motor is re-installed into your system.
1. The pump case flange face is repaired or manufactured to suit site connection with the pump case, and should be done so with a Flexitallic gasket or o-ring depending on design. The pump case connection is prepped for shipping, either wrapped in plastic or fitted with a top hat/transit canister (supplied by the customer), in order to ensure the gasket face is protected. Plastic is used when the pump is shipped and stored dry, and the transit can is used when filled with long term storage fluid. Neither the wrapped plastic nor the transit can are designed to withstand your boiler/system pressure.
2. The motor cover flange is repaired or manufactured to be fitted with a Flexitallic gasket or o-ring and is designed and assembled to withstand system design pressure. Repaired motors do not have a hydro test performed at HT.
3. The fill and drain port is a flanged or bare pipe connection depending on the plant’s connection to a water supply source. These connections are not hydro-tested during repairs, but they are hydro-tested during new manufacture of motor case or covers. These ports will be wrapped in plastic, unless the motor is filled for long term storage, in which case these ports will be fitted with non-pressure rated “shipping only” blanking flange (painted yellow or orange) ), “shipping only” gaskets, and “shipping only” hardware. Neither the plastic nor the “shipping only” parts are designed to withstand your boiler / system pressure.
4&5.The two heat exchanger connections (inlet and outlet) are also flanged or bare pipe connections depending on the customer’s connection to the heat exchanger. HT inspects these connections for visual damage, and if indications are noted, a dye penetrant inspection is performed and the connections are repaired. These connections are not hydro-tested during servicing, but they are hydro-tested during the new manufacture of the motor case or covers. These connections will be wrapped in plastic, unless the motor is filled for long term storage, in which case these connections will be fitted with non-pressure rated “shipping only” blanking flange (painted yellow or orange), “shipping only” gaskets, and “shipping only” hardware. Neither the plastic nor the “shipping only” parts are designed to withstand your boiler/system pressure.
6. Some motors have purge connections on the motor case near the hot neck (this applies to boiler water circulating pumps only). Motors sent to HT with a pressure rated flange and hardware provided on the purge connections will be re-installed with a new pressure rated Flexitallic gasket and the same flange and hardware. For purge connections that do not have pressure rated flanges sent in with the motor, the connections will be wrapped in plastic, unless the motor is filled for long term storage, in which case these connections will be fitted with non-pressure rated “shipping only” blanking flange (painted yellow or orange), “shipping only” gaskets, and “shipping only” hardware. Neither the plastic nor the “shipping only” parts are designed to withstand your boiler/system pressure. Also, purge connections that are not utilized can be blanked-off with a threaded pipe plug and seal welded to eliminate future concerns.
SAFETY NOTE:

Use of temporary “shipping only” flanges, gaskets or hardware in high temperature, high pressure boiler operation service could potentially fail and cause steam breaches, which will cause serious motor damage, and/or serious injury. These connection need to be properly checked by the customer to make sure that pressure rated flanges, gaskets, and hardware are used. In addition, these connections need to be visually verified by the customer via the boiler hydro-test pressurization test, prior to the boiler being pressurized for operation with hot water.
HT Responsibility:
- Prepare the 6 flange connections to be able to accept appropriate pressure rated flanges, gaskets, and hardware
- When the pressure rated parts were provided with the motor by the customer, re-install the appropriate pressure rated flanges, gaskets, and hardware
- When the pressure rated parts were not provided with the motor by the customer, prepare those flange connections to be protected for shipment to the customer using plastic or temporary “shipping only” non-rated flanges and gaskets
Customer/Operator Responsibility:
- Prior to installing pumps, check the motor case and pump cases for temporary “shipping only” flanges (painted yellow or orange), gaskets, and hardware.
- Remove temporary flanges, gaskets, and/or hardware and replace them with pressure rated flanges, gaskets, and hardware.
- Verify flange connection integrity of all 6 areas as part of the plant’s boiler hydro-test pressurization test, prior to the boiler being pressurized for operation with hot water.
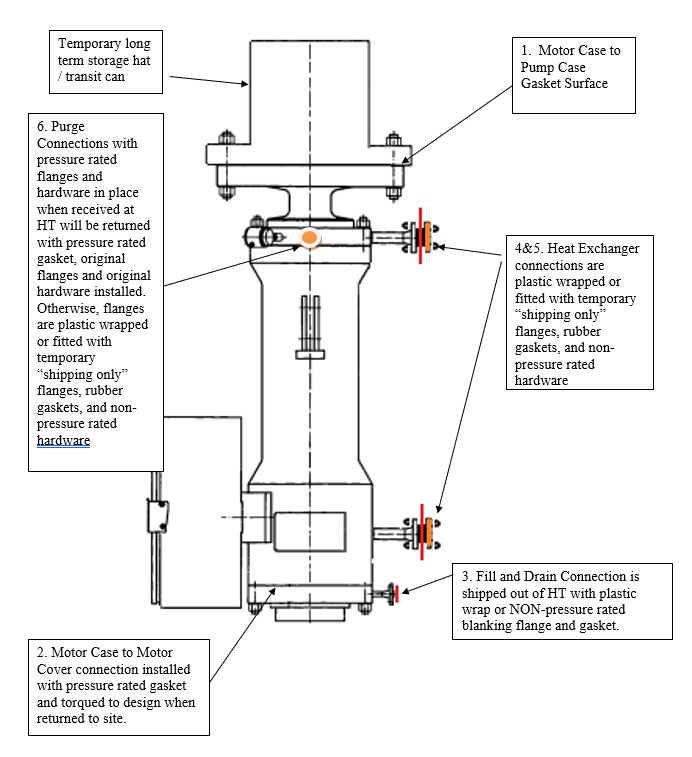