Download this Case Study:
Introduction:
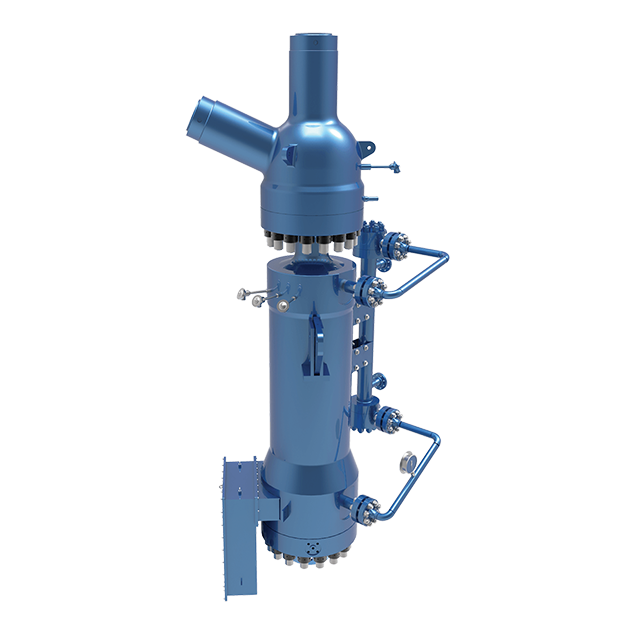
The rise in total generation capacity of renewable energy sources such as wind and solar is resulting in traditional “base load” coal generation plants being more frequently used to follow fluctuating electricity demand i.e. “peak load” operating. This change in operation has a consequential effect on the power plant equipment as it is now being subjected to operating conditions it was not originally designed for.
In the context of this paper, the term “base load” is used to mean a plant operating at a stable electrical output for a sustained period of time. This is typically at or near the peak efficiency of the plant. What this means for the Boiler Water Circulating Pump (BWCP) in that plant is that there are minimal thermal cycles and, hence minimal cyclic thermal stresses. In addition, the equipment is able to be operated at a stable, constant condition as opposed to frequently being started and stopped or ramped up and down along the pump curves.
In contrast, the terms “peak following” or “peak load” mean operation that fluctuates up or down to match the short term electrical grid power demand. This plant cycling means the BWCP’s see increased thermal cycling and either starts/stops or fluctuating operation along the pump curve as the plant flexes to provide a changing electrical demand. The fluctuation of boiler evaporation rate and, in some cases, boiler pressure has an effect on the operation of the BWCP.
The Boiler Water Circulation Pump is typically used in forced circulation drum boilers to provide the necessary head (pressure) to overcome the frictional losses encountered in the boiler tubes. This allows the water to circulate through the boiler to be turned into steam and used to generate electrical power in the turbine-generator set. The BWCP is a glandless sealless combined motor and pump. There is no dynamic mechanical seal between the motor and pump and they share a common shaft. The motor and pump are designed for the same system pressure; however, the motor is maintained at a cooler temperature using a thermal barrier and a heat exchanger. A Boiler Water Circulating Pump typically uses a wet stator design. A typical BWCP is shown below. The combination of a fluid filled electrical motor and pump makes this a unique component when considering all the areas affected by changing plant operation.
So what does it mean for my Boiler Water Circulating Pump? Frequent changes in the operation of the Boiler Water Circulating Pump affects multiple areas within the BWCP. Each area is discussed below.
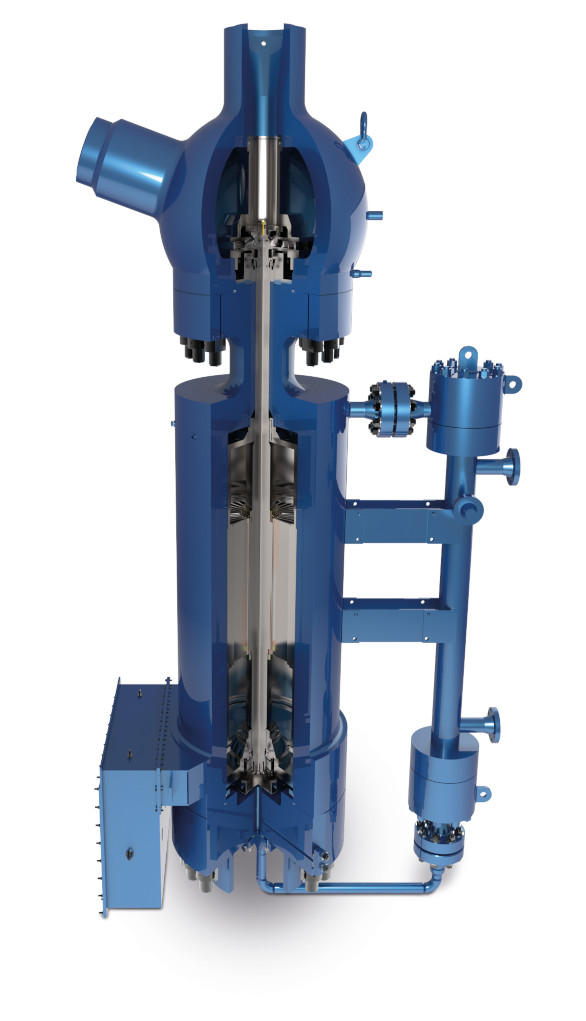


















Thrust bearing
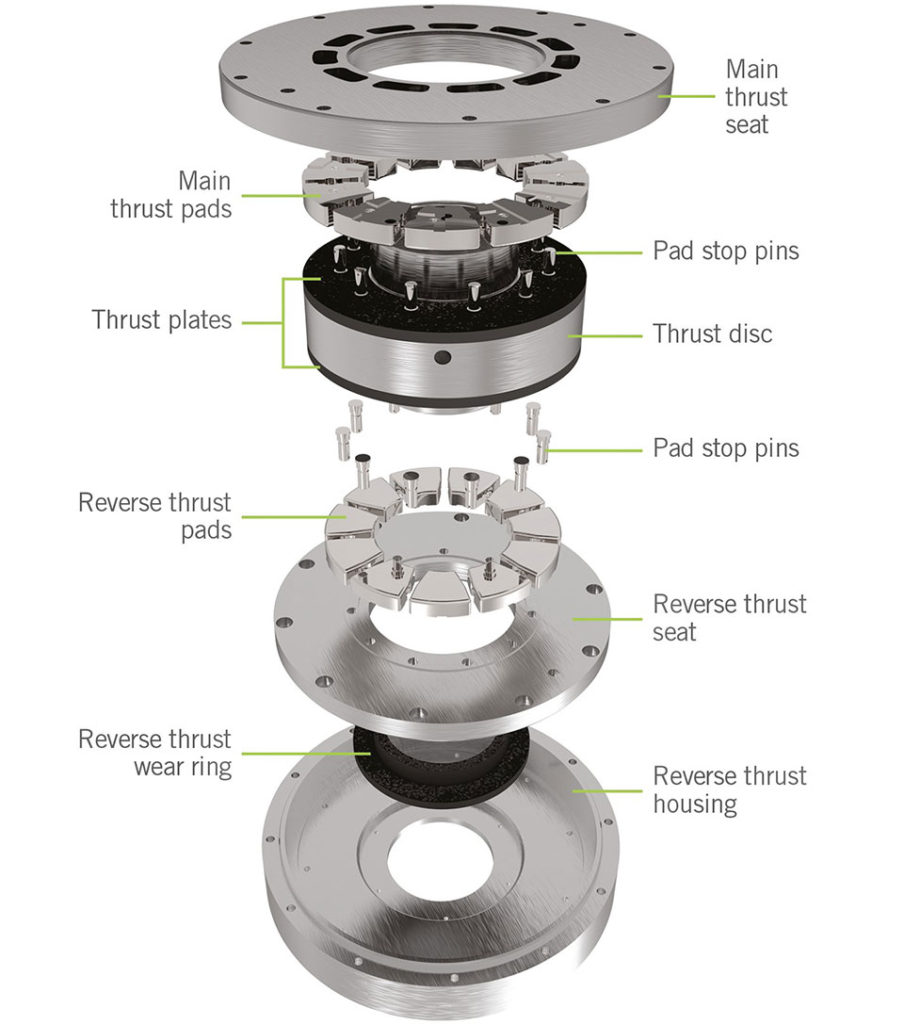
A typical BWCP is supported axially using a hydro-dynamic thrust bearing. The bearing works by using a water wedge that is formed between the thrust disc (which is keyed to the shaft) and tilting thrust pads. The thrust bearing is designed to accommodate the weight of the rotor and additional thrust loads from the pump including a suitable design safety factor. When the motor starts up the hydraulic lift from the impeller lifts the rotating assembly upwards to establish a film of water between the thrust bearing surfaces during stable operation. When the BWCP is shut off the rotor loses the hydraulic lift and returns down to the reverse thrust bearing. Initially, during start-up there is an insufficient fluid film between the non-metallic bearing and the thrust pads therefore the friction between the pads can cause a small amount of material wear. This reduces the thickness of the bearing material and begins to open up the distance the rotor can travel (“rotor end float”). This means that the rotor is traveling further every time the motor is de-energized resulting in a larger thrust being absorbed by the bearing.
Long term cycling can result in damage to the thrust bearing that requires accelerated maintenance or in some cases causes catastrophic failure of the thrust bearing requiring extensive repairs. It is recommended to perform a thrust inspection every three years and then develop an asset management strategy based on the “as-found” condition of the thrust bearing components. Monitoring pump performance and critical clearances, as found during inspections, allows customers to better understand the wear associated with their plant running regime and adjust maintenance cycles (as far as reasonably practical) to maximize the life of the BWCP.
If you have a single thrust bearing you should consider upgrading to a double thrust arrangement as detailed here. Your BWCP operating and maintenance manual tells you the thrust configuration of you BWCP. If you can’t find it contact us, and we can easily advise.
Radial Bearing
Similar to the thrust bearings, the radial bearings in the BWCP use hydrodynamic bearings. The radial bearings are located at the thrust end and pump end of the motor.
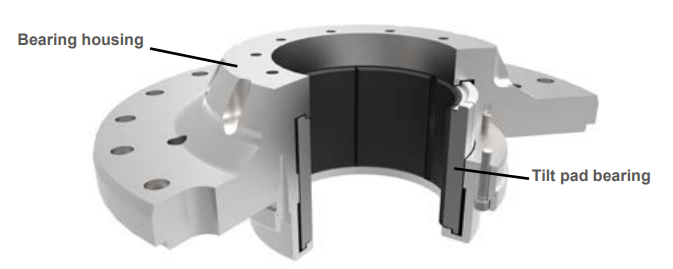
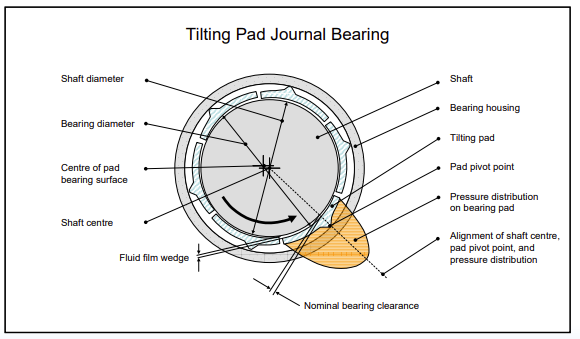
Accurate alignment of the radial bearing is controlled by manufacturing tolerances of the stator housing and motor case. The radial bearings are sized to absorb loads from unbalanced magnetic pull (UMP) on the rotor, hydraulic fluctuations in the pump creating unbalanced loads and ensure safe rotor dynamic characteristics. When the BWCP starts there is insufficient fluid film between the journal sleeve and the bearing surface. Like the thrust bearing this creates wear on the pads resulting in lost material and larger clearances. This is a propagating effect as the bearing wear allows the rotor to deviate from the center axis of the stator which increases the UMP and hence increases bearing wear. Increased bearing wear allows the rotor to deviate away from alignment with the stator and hence the damage propagates due to worn radial bearings. If the bearing clearances become excessively large under extreme conditions the UMP during start-up could cause rotor to stator contact due to bending in the rotor. This could cause damage to the stator and rotor lamination packs resulting in the need for restacking.
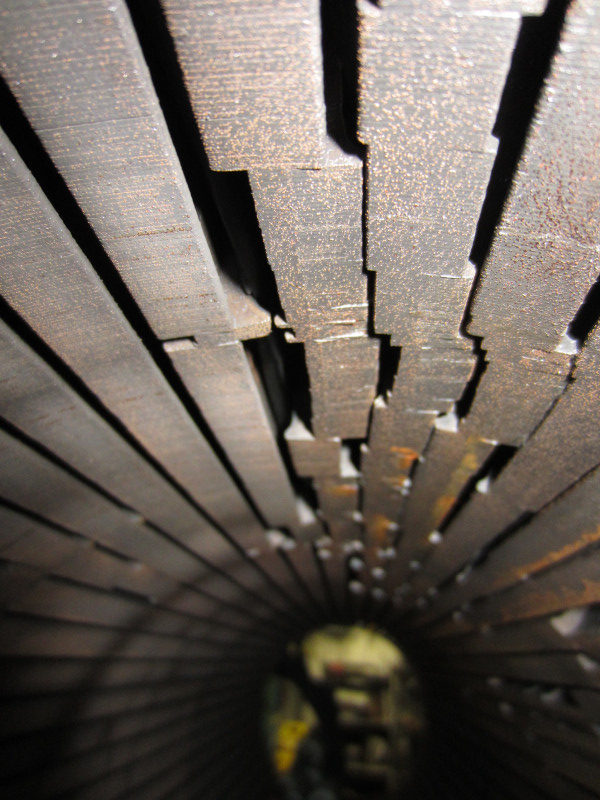
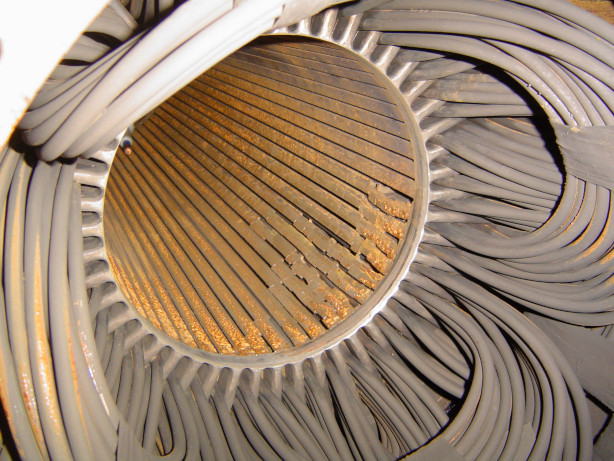
Impeller wear ring
The impeller wear ring is set with a pre-determined diametrical clearance to the pump case/diffuser wear ring in order to control the pressure drop across the surface and the amount of fluid recirculated. In addition, the distance from the pump case to the motor case mating face and end of the impeller (known as the “A” dimension) is controlled to ensure no axial contact. Under scenarios where the plant is quickly changing load or fully starting and stopping the motor, there is typically a temperature difference between the pump case and rotating assembly. Depending on that temperature differential the impeller and pump case will grow or shrink at different rates from each other. This reduces the wear ring clearance and can cause contact. In severe situations, binding of the rotating assembly to the static wear ring can occur. Frequent load changes will cause accelerated degradation to the wear rings. This increases the clearance and reduces efficiency (due to increased recirculation) but, more severely, shortens the life of the wear rings and can cause major damage to the impeller and rotating assembly. Excessive contact of the impeller to pump case can bend the rotor, damage the radial bearings and have consequential effects of damaging the stator windings due to debris being circulated through the motor.
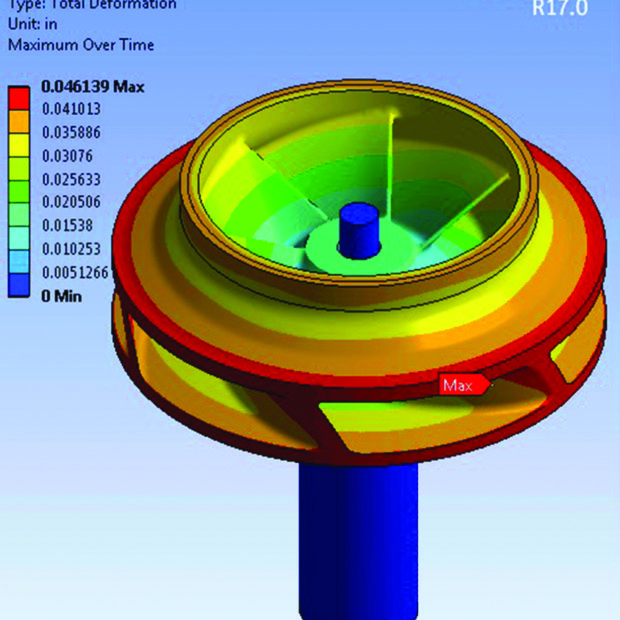
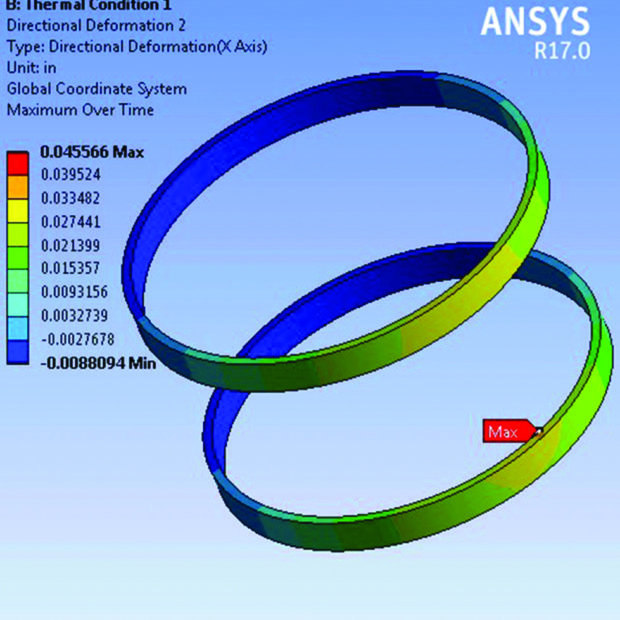
Pump case
The pump case on a BWCP is welded into the pipework and typically made from a thick-walled carbon steel casting. Frequent thermal cycling on the pump case due to changing operating loads subjects the pump case to thermal stresses as the pump case tries to expand freely, however, is constrained by the pipework and connection to the motor. Frequent thermal stress cycling can present problems with fatigue crack development at critical regions such as changes in thicknesses, nozzle regions, and welds. Operators undertaking frequent load changes and thermal cycling should ensure to inspect pump cases for the development and propagation of cracking. If the pump case welds are not part of a maintenance program associated with “high energy pipework” they should be included in the periodic inspection of the pump case.
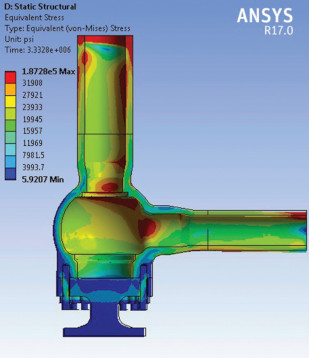
The image above shows the highest stressed areas of a representative pump case and is the area that should be inspected first for fatigue cracking.
The below images show cracking that was discovered in actual BWCP pump cases. The cracking caused extended downtime for the plants involved.
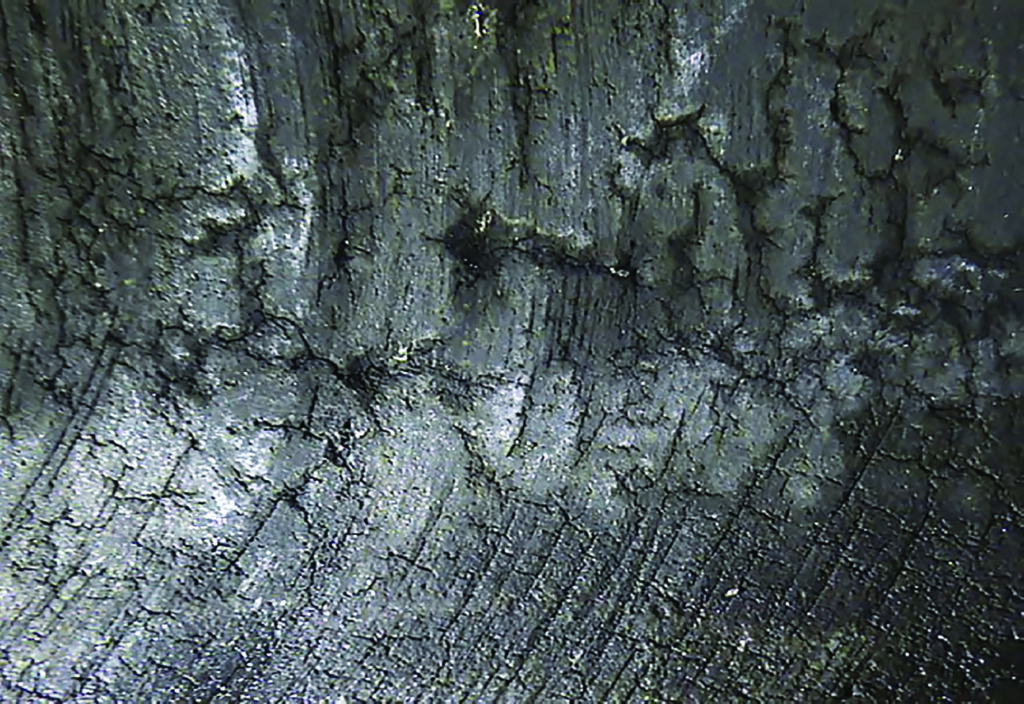
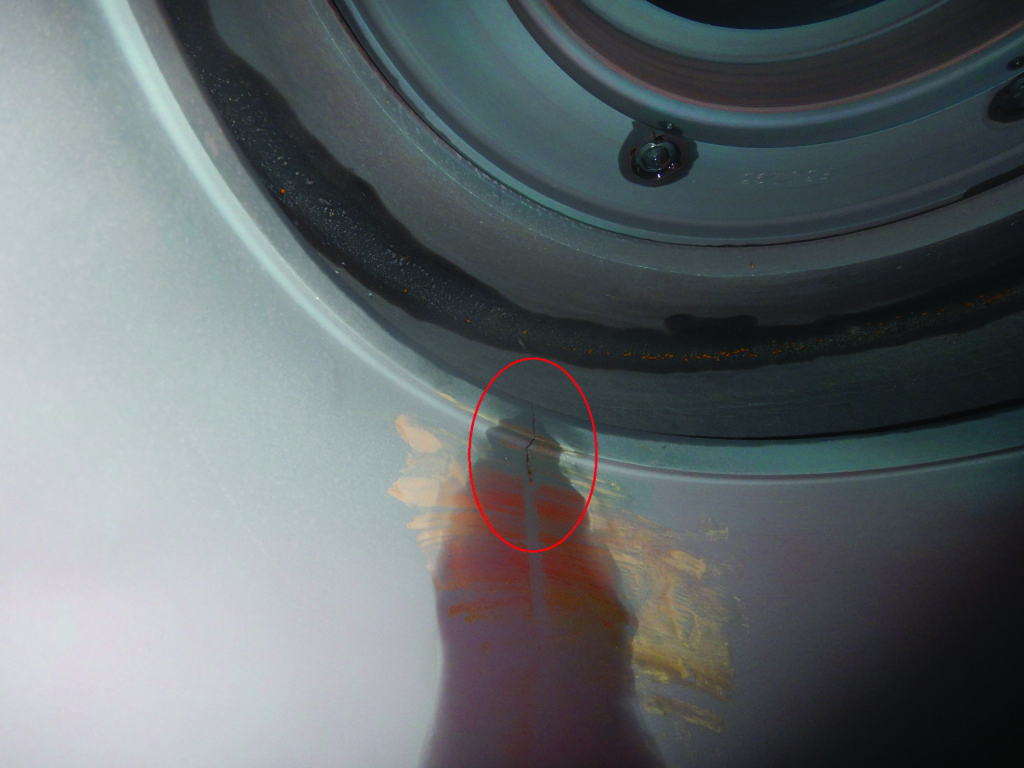
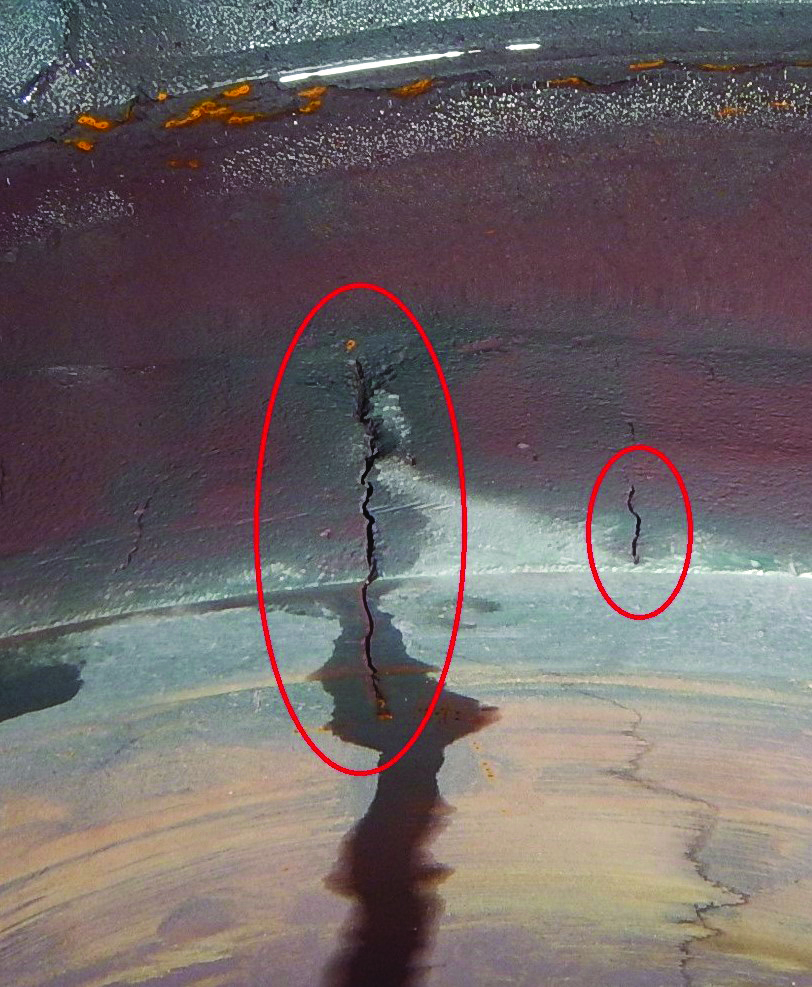
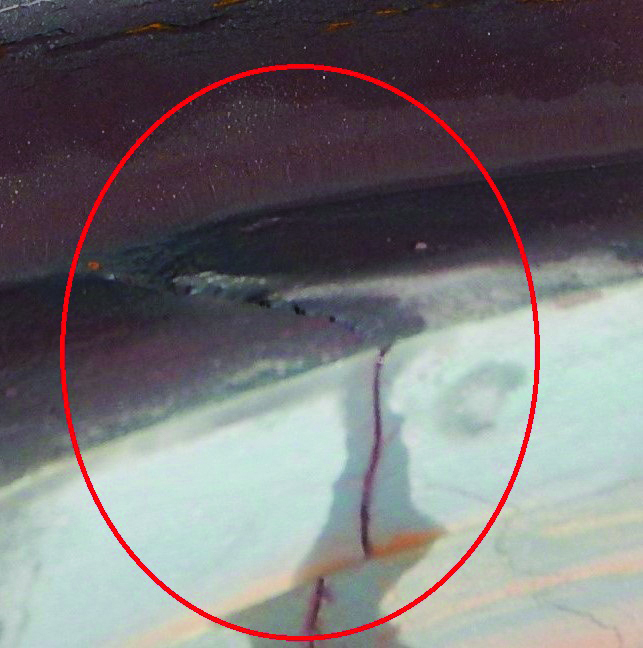
Electric Motor
Motor in-rush current
The electrical motor is under the most stress during a start-up. The in-rush current of a typical BWCP is approximately 4.5-5 times the full load current. The majority of BWCP’s are Wet Stator Units (WSU) which means the rotor and stator are submerged in water. Wet Stator Units use cross-linked polyethylene (XLPE) insulating material to insulate the copper wire from the water in the stator. This large current causes the copper wire to heat up having a short-term negative effect on the insulation. Every time a motor is started it reduces the lifetime of the insulation leading to an increased risk of an insulation failure.
Mechanical rub/fretting
When the stator is initially wound, the cable in the slots are wedged together to keep them packed tightly together. With the normal operation of the electrical motor, the cable in the slots bunch together and pull to the outside of the stator due to the magnetic forces in the motor. This can have the effect of the cable becoming looser in the stator slots allowing additional cable movement. A typical 4 pole wind is shown below.
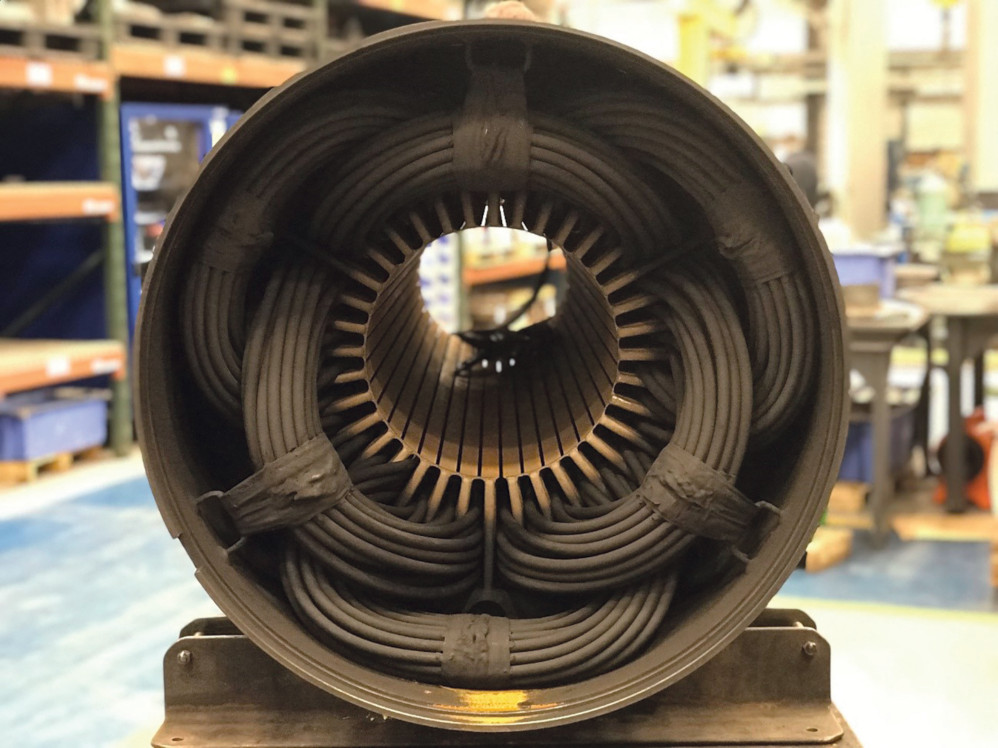












During the start-up of the electric motor, the cable in the end turn phases exert magnetic forces on cables in adjacent end turn phases causing the end turns to move and vibrate. The outer coils are pushed towards the outside of the stator shell and the inner coils are pulled towards the rotor. The end turns flex with the changing magnetic fields induced by the incoming current. Over time with high numbers of starts to the motor (more than originally designed), this end turn cable movement, combined with the increased movement in the slot can result in the cable rubbing on the stator endplate. If this behavior continues the cable insulation wears down until an insulation failure occurs (as shown below). On some occasions, the insulation failure causes an electrical arc which damages the stator end plate and stator laminations. This can mean a full or partial restack is necessary along with a stator rewind resulting in extended motor downtime and significant repair costs.
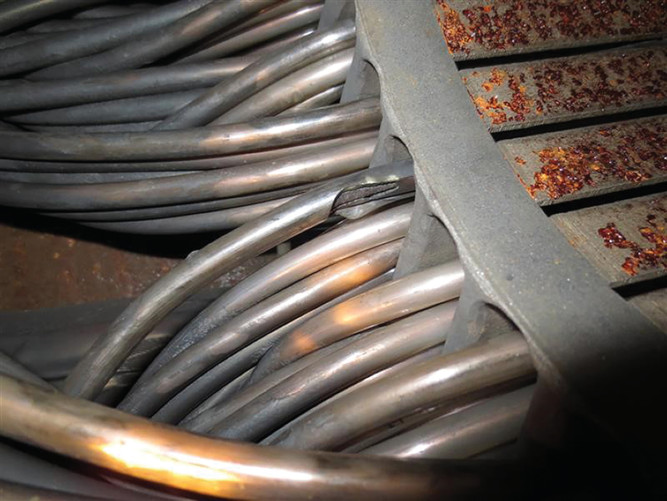








Unbalanced Magnetic Pull (UMP)
Unbalanced magnetic pull (UMP) occurs when the centerline of the rotor does not perfectly line up with the centerline of the stator. Upon start-up, the electric motor acts like a magnet pulling the rotor approximately in the direction of the smallest airgap. This can cause a static or dynamic eccentricity in the rotor motion. As mentioned above under the “Radial Bearing” section, under extreme conditions with sufficient bearing wear there could be rotor to stator contact.
Insufficient NPSHa
Scenarios have been observed where during fluctuating plant load (MWe output) or unplanned shutdowns the BWCP experiences cavitation. This can be caused by a few different scenarios:
- The NPSHa has decreased because the steam drum is being vented or the drum pressure is lower than normal operation. In this scenario the pressure on the liquid surface in the drum is reduced. This means that the only NPSHa to the pump is the static elevation of the liquid above the pump minus any frictional losses. This has been shown to be insufficient causing cavitation at the pump suction.
- The system resistance which consist of the static elevation pumped plus the resistance of pipe fittings, valves etc. has decreased. The pump will increase its flow until its developed head intersects with the new system resistance curve. As NPSHr rises with flow there may not be enough NPSHa to satisfy NPHSr.
- The BWCP’s are used to help force-cool the boiler in the event of a tube leak. As the pressure and temperature in the boiler are reduced to come off to repair the tube leak the BWCP’s are left running to force additional flow through the boiler. This results in a drop in NPSHa which may drop below NPSHr.
In these scenarios cavitation will likely cause the following damage:
- Damage to main and reverse thrust bearing due to loss of hydraulic lift in the impeller as a consequence of vapor entering the suction. This has the effect of the rotating assembly shuttling
between bearings faces causing damage. - Damage to impeller from pumping non-compressible air pockets. This often sounds like marbles being pumped through the impeller and can cause pitting on the impeller surface as the bubbles collapse. More commonly damage is attributed to increased vibration resulting in increased wear on the radial and thrust bearings.
A more detailed explanation with examples can be found here: Power Plant Cycling: Its effect on NPSHa and the damage it causes to Boiler Water Circulation Pump (BWCP) thrust bearings
Other consideration for older motors
Changes to system resistance
Originally when the power plant was designed a system resistance applicable to the BWCP was calculated based on the designed static head plus the frictional losses due to pipework, valves, orifices, etc. in the system. The frictional losses aspect of the calculation varies with the square of the flow. The pump will operate at the point where the pump curve and system curve intersect. The pump curve only changes if the speed of the motor is changed or the impeller diameter is changed, both of which are very uncommon on BWCP’s. Changes to the system such as modified valve arrangements, changes to pipework configuration or diameter, degradation of drum baffles, etc. all have an effect on the system resistance which in turn dictate where the pump operates along its pump curve. This can result in the pump being operated away from its originally designed duty point which can cause increased vibration in the BWCP. Increased vibration will result in accelerated damage to the radial bearings and thrust bearing. If the system resistance has increased the pump will run back on the pump curve i.e. lower flow, higher head. The increased differential pressure across the impeller can cause increased thrust on the rotating assembly accelerating bearing wear.
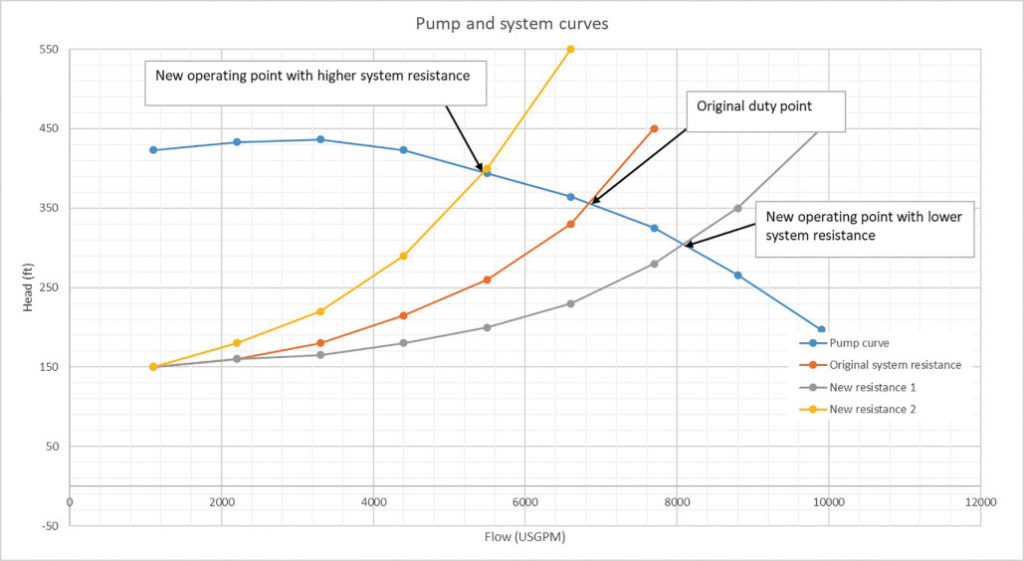
Discharge valve inspection
The BWCP either has a single discharge or a double discharge from the pump case as shown below.
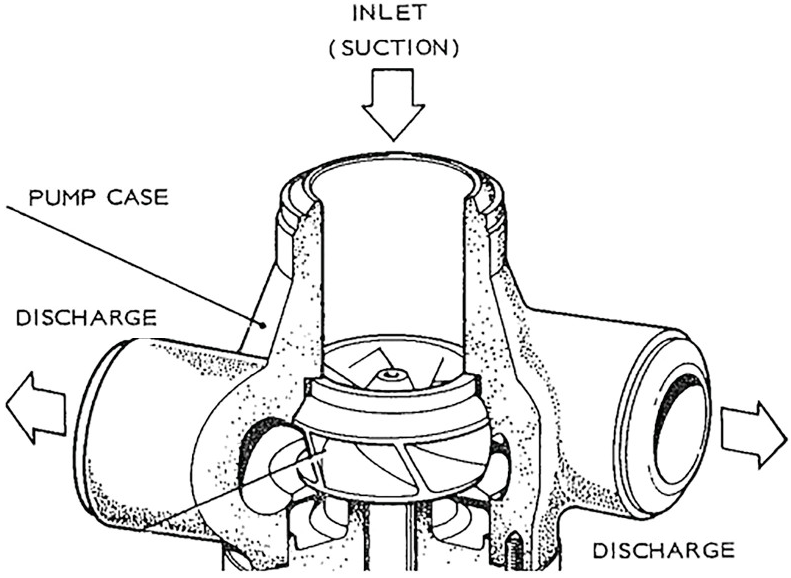
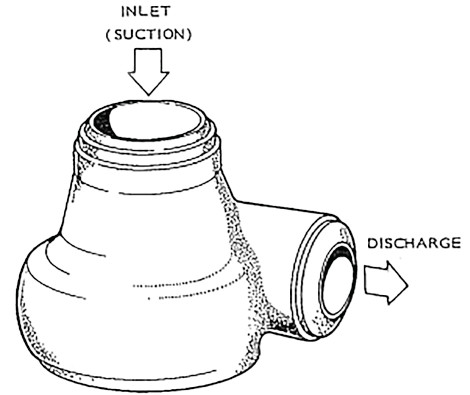
In both cases, the discharge pipework has an isolation valve to isolate the BWCP from the boiler. If the discharge valves are not well maintained they can partially close when they are not supposed to and this has a negative effect on the BWCP. If the discharge valve is partially closed with the pump in operation it will force the pump to operate back on the pump curve with a large differential pressure across the pump. The increased differential pressure across the impeller can cause increased thrust on the rotating assembly accelerating bearing wear. In the case of double discharge pump cases, if one of the discharge valves has not been maintained and floats to a partially closed position this affects the alignment of the impeller within the pump case. The impeller and rotating assembly will tend to locate away from the discharge with the partially closed valve. The off-center alignment will cause uneven wear on the radial bearing which, as discussed previously, will increase the UMP on the rotor.
Leaking pump flanges
Long term neglect of the pump case and/or motor cover studs of a BWCP can cause them to corrode and seize in place. New pump case studs have a zinc phosphate coating to improve corrosion resistance and paint adhesion followed by a high-temperature anti-friction coating. If the pump case/motor case gasket has leaked or the plant environment is frequently subject to water the studs can corrode and bind in place. Often the only way to remove the studs is to cut them out. This causes an unnecessary expense for the plant requiring them to purchase new studs, often on an expedited basis.
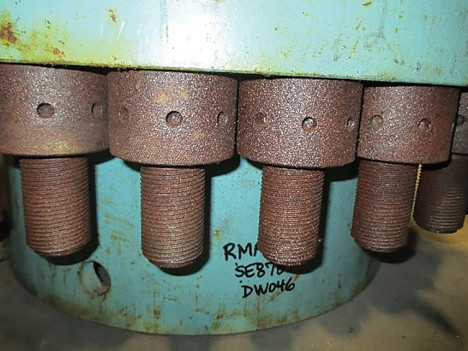
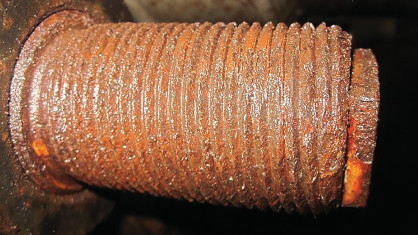
Conclusions
As it can be seen from the above review, cycling plants present a different set of problems for BWCP’s than they were originally designed for. The way in which the BWCP is operated has a major impact on the reliability and longevity of the components. As plants are being asked to operate in increasingly flexible ways it is important that the plant engineers understand the impact on the BWCP to help mitigate and reduce the likelihood of failure. An increased and targeted maintenance regime helps to support the long life of the BWCP.
Hayward Tyler is able to provide an in-depth analysis of your operating regime to analyze how it
is impacting your BWCP. See our case study “Thermal Stress and Fatigue Life Assessment
Validates Flexible Plant Operation” as an example.
Categories: White Papers