Download this Case Study:
Hayward Tyler analyzed the effects of various power plant operating scenarios on a Boiler Circulating Pump (BCP)
Boiler Circulation Pumps are used in forced circulation boilers to circulate the water around the waterwalls or economizer. Due to high boiler pressures, the pump cases are often thick-walled components. Power plants can find themselves in a boiler operating situation where the differential temperature between the pumped fluid and pump case of a BCP exceeds the standard recommended limit. This has the potential to impact the plant’s ability to provide the required electrical generation (MW) while it waits for the pumped fluid/pump case differential temperature to return to within the allowable range. This can result in significant lost revenue.
Hayward Tyler was contracted by a major Engineering, Procure and Construction (EPC) company to assess the expected degradation to a BCP based upon 22 different plant operating conditions. The operating conditions varied from cold starts/stops to hot start/stops and trip conditions. Our engineers carried out thermal stress analysis and fatigue life calculations using Finite Element Analysis (FEA) to quantify the degradation expected on the BCP. This included assessing for component interference due to rapid thermal expansion and a calculated fatigue life of the main components due to thermal shocking. The results showed that all operating scenarios would be acceptable except one, which would result in a mechanical rub between the impeller and diffuser wear rings. This scenario could cause significant damage to the BCP if it is was undertaken by the plant. In addition, Hayward Tyler was able to identify the highest stressed areas of the pump case based on the FEA results. This can be used when carrying out local inspection of the pump case.
The analysis allows plant operators/owners to better understand the damage to their equipment based on how they want and need to operate the power plant. They are able to make informed decisions on operating regimes by understanding the impact to their BCP.
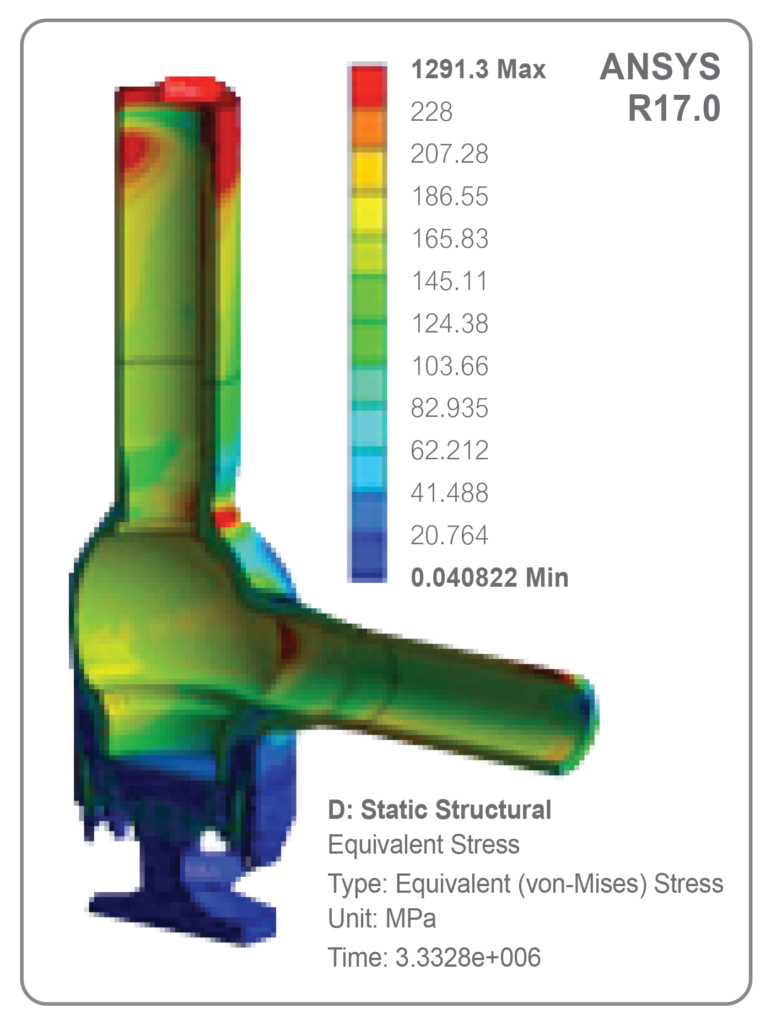
Project Summary
SITE/LOCATION:
- Super Critical Power Plant
SCOPE OF WORK:
- Finite Element Analysis using ANSYS
- Assessing 22 different operating conditions
- Thermal stress/growth interference analysis
- Thermal fatigue analysis using FEA and verified using hand calculations
- Highlighted problematic operating scenario
- Highlighted critical areas for local plant inspection
BASIC PUMP/MOTOR DESIGN DETAILS:
- Vertical, Motor Under, Glandless Wet Stator Circulating Pump
- Rated Flow: 8015 gpm
- Rated Head: 345 ft
- Design Pressure: 4675 psig
- Design Temp: 657 ° F
- Rated Power: 938 hp
Project Data Sheet (analysis based on)
Product | Boiler Circulating Pump |
Quantity | One (1) |
Codes and Standards
Model Standards | ASME Section VIII Div I |
ASME Section VIII Div II | |
ABSA AB-520 | |
1-D Analysis | ASME Section VIII Div II |
Static Linear Elastic Study | ASME Section VIII Div II |
Fatigue Assessment | ASME Section VIII Div II |
Yield Stress Properties | ASME Section II |
Motor Details
Motor Rating | 938 HP, 700kW |
Service Factor | 1.0 |
Nominal Speed | 1750 rpm |
Power Supply | 6600 V / 3 ph / 60 Hz |
Motor Full Load Current | 82.6 Amps |
Starting Current | 434 A |
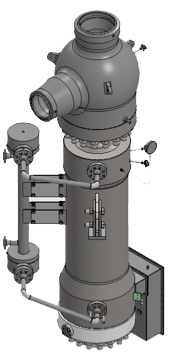
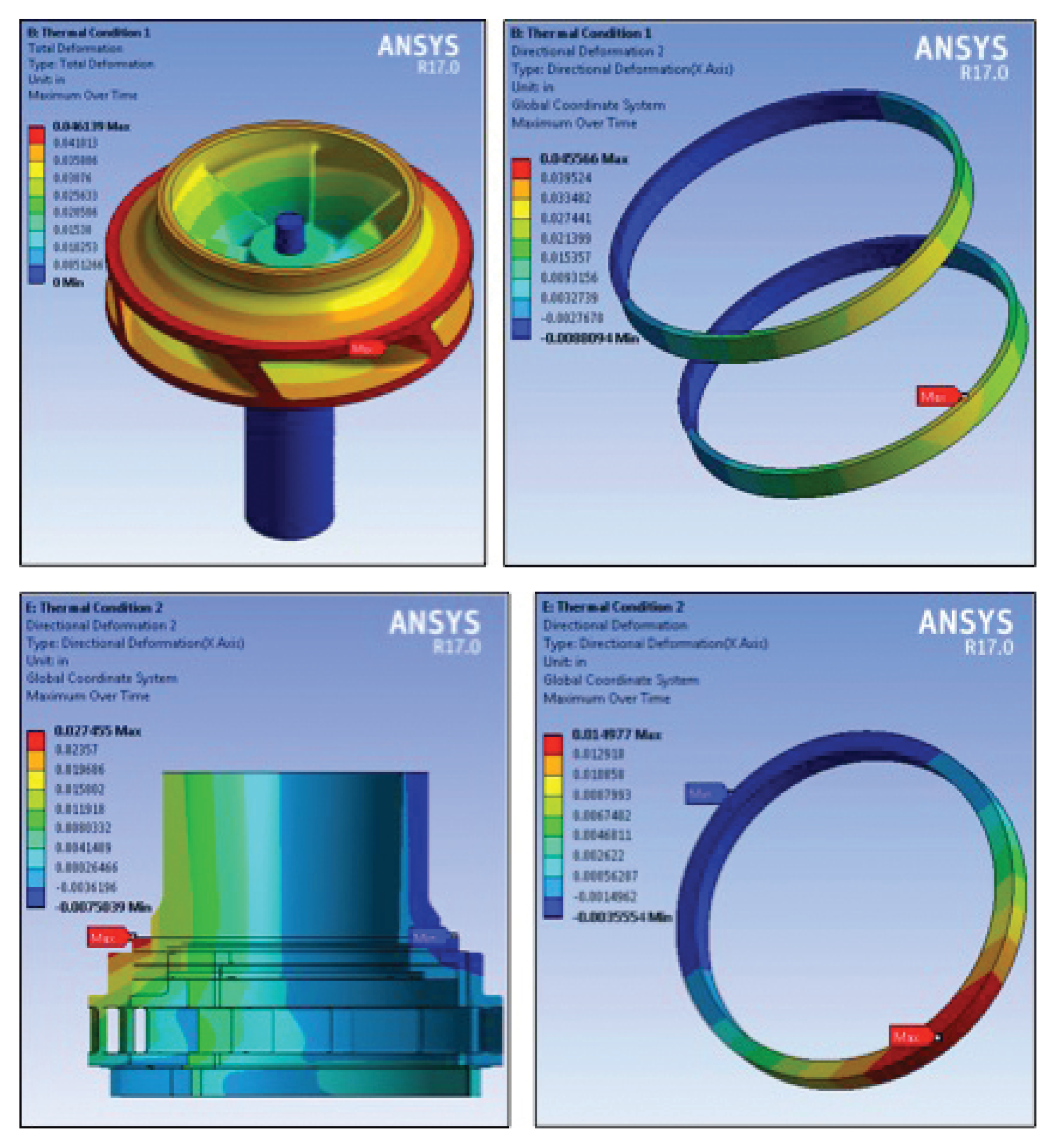
Pump Details
Pump Type | Centrifugal, Single Suction, Single Discharge |
Pump Size | 14” Suction x 14” Discharge with 21” Impeller and Diffuser |
Fluid Pumped | Boiler Water |
Rated Flow | 8015 USgpm (1820 m3/hr) |
Rated Head | 345 ft (105 m) |
Design Pressure | 322 bar |
Design Temperature | 657° F (347° C) |
Hydrostatic Test Pressure | 7013 psig (484 bar) |
NPSHr | 105 ft (32 m) |
Specific Gravity | 0.623 |
Weights (Approximate Dry)
Pump Case | 7112 lbs | 3226 kg |
Complete Motor and Rotating Assembly | 24,472 lbs | 11,100 kg |
Heat Exchanger | 1732 lbs | 786 kg |
Total | 33,318 lbs | 15,113 kg |
Categories: Case Studies